中川政七商店のものづくり実況レポート。ふわふわの毛布とルームウェアを生み出す、毛布のまち 大阪 泉大津へ
エリア
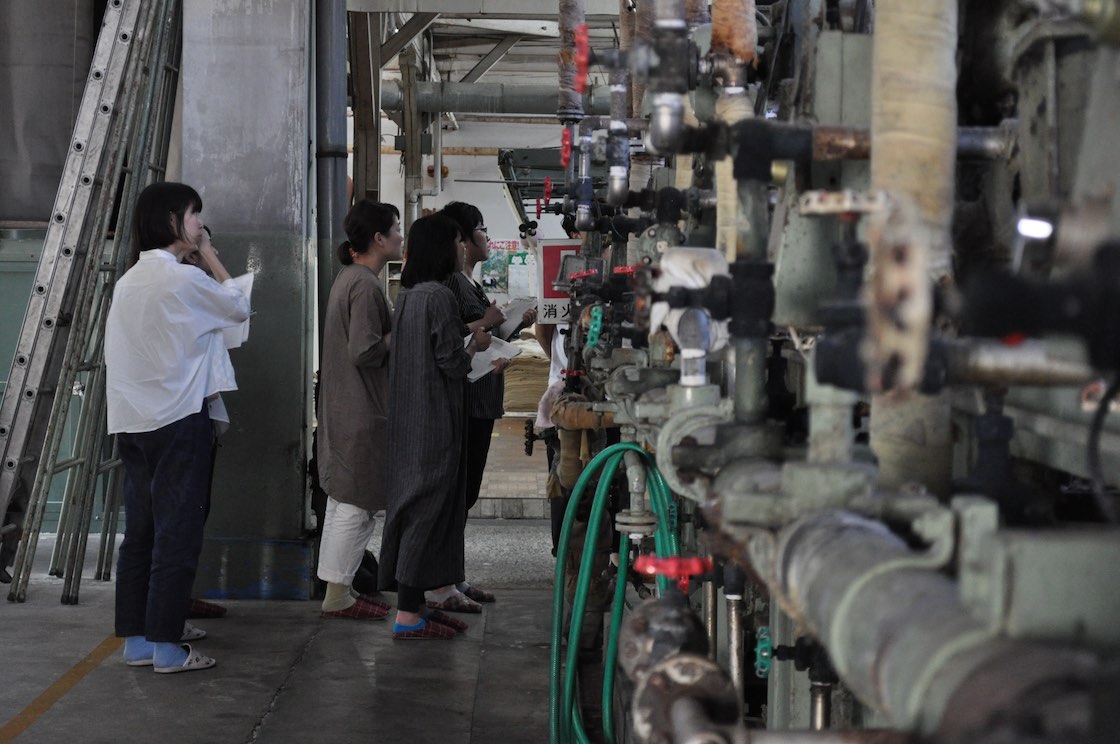
中川政七商店の人気アイテムのものづくり現場をスタッフが実際に訪ねる「さんち修学旅行」、今回は大阪へ。
前編ではロングセラー商品「もんぺパンツ」のさらさらのはき心地の秘密を、大阪堺に訪ねました。
後編はその足で向かった毛布のまち、泉大津の今新毛織株式会社さんのものづくりをご紹介。
これからの季節にぴったりの、あたたかなオリジナル毛布やルームウェアの生地を作っていただいています。
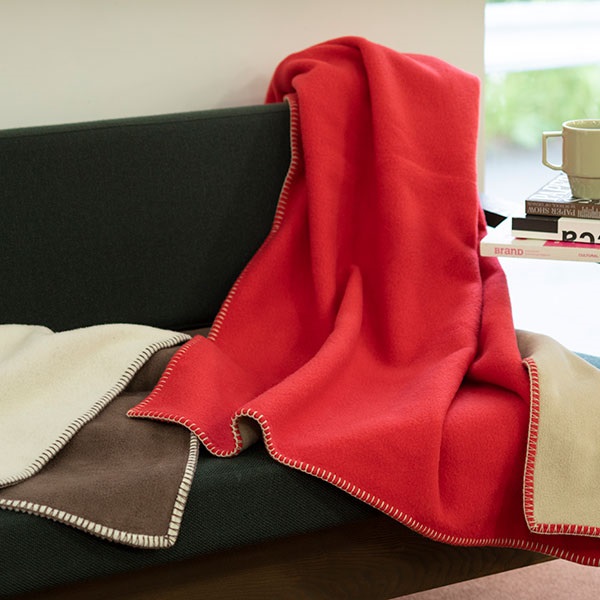
▲泉大津の2重織毛布
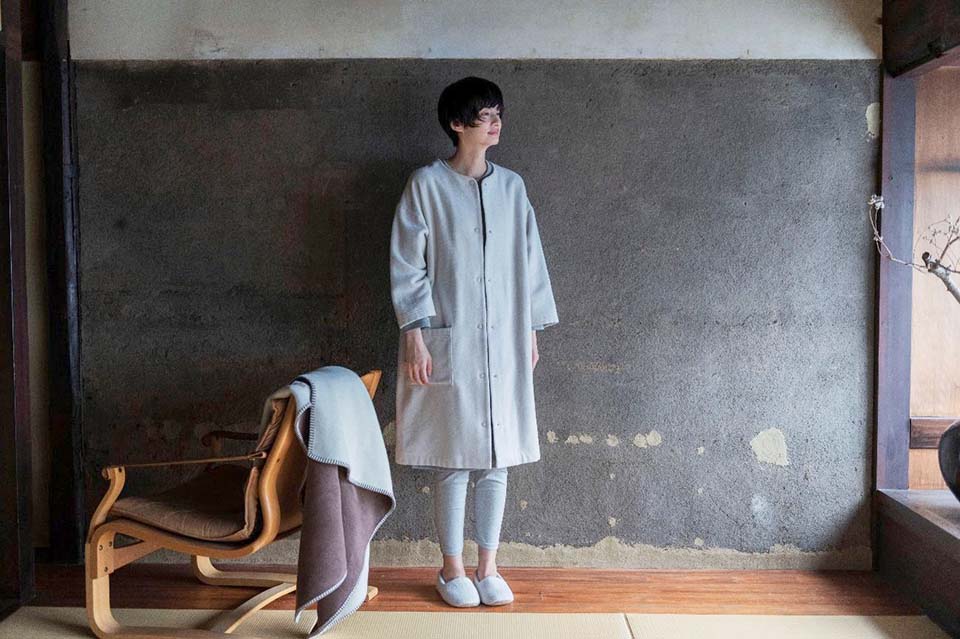
ここからは、ルクアイーレ店店長の福井がお届けします!
日本最大の毛布の産地、泉大津へ
毛布の産地は泉大津やその周辺で全国の9割を締めているとのこと。日本で最大の産地と言えます。
その中でも、今新毛織さんは、織りから染色、整理加工、縫製までを一貫生産する国内唯一無二の工場。
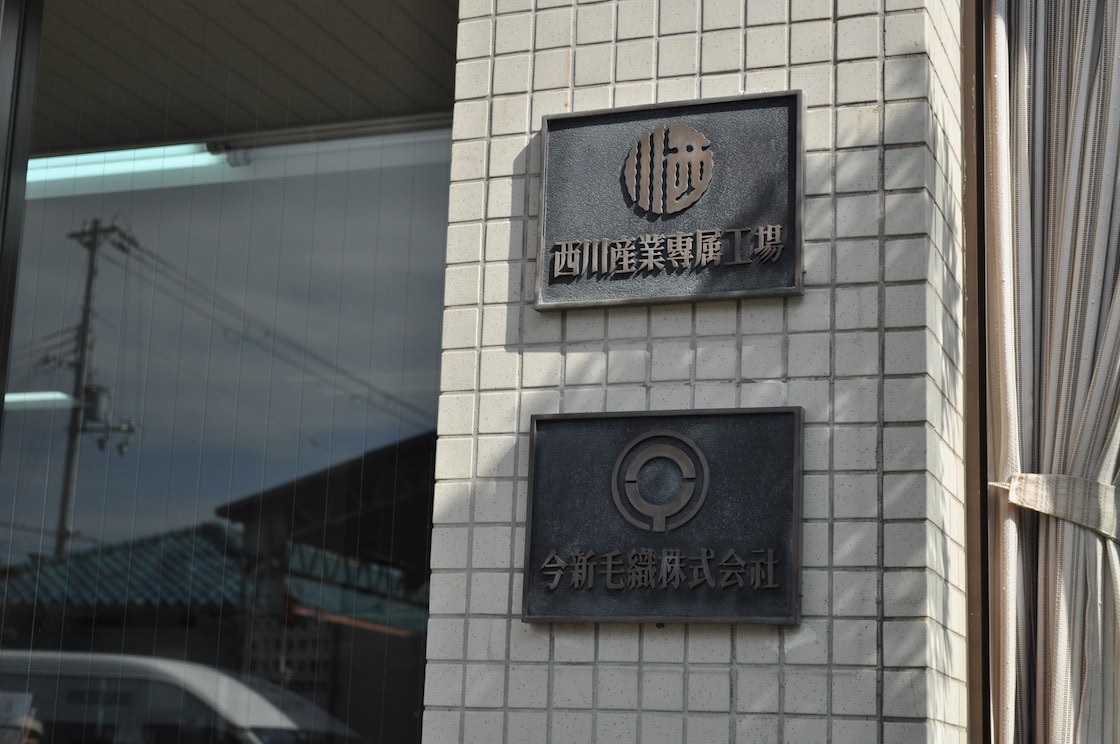
本日は毛布ができるまでの工程を見学させていただけることに。柔らかい毛布はどのように作られているのでしょうか…
本日は今井社長と横田専務にご案内いただけることに。
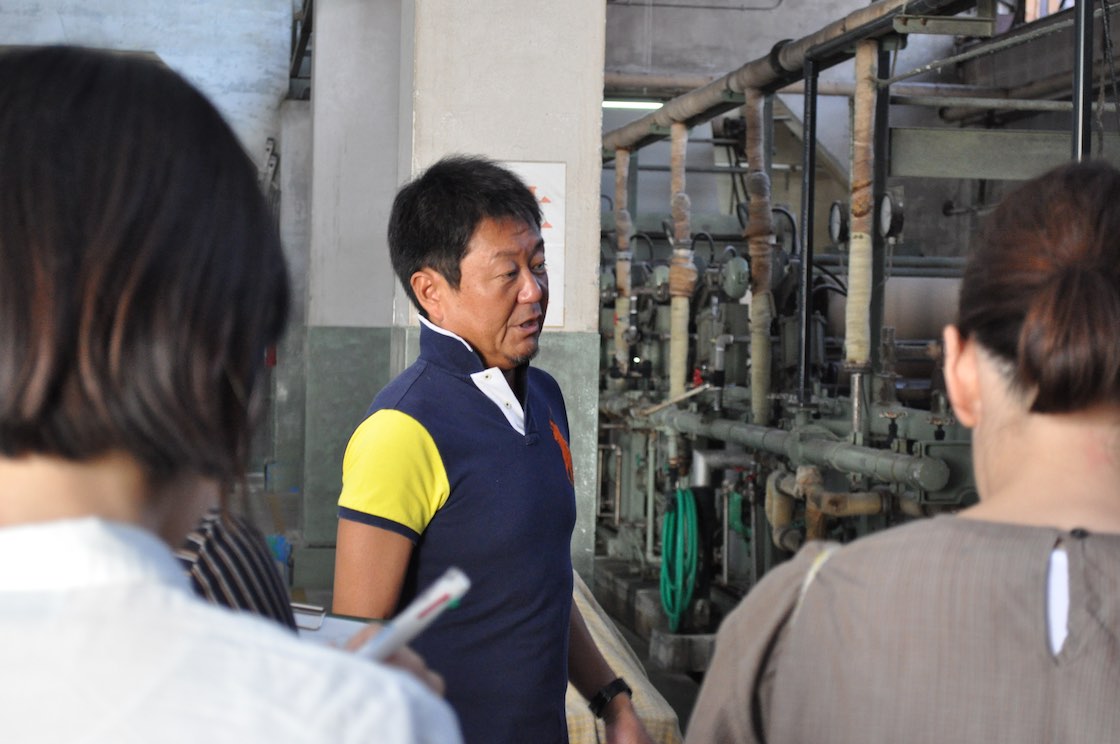
▲工場を案内くださった今井社長
毛布はつくり方によって織毛布、マイヤー毛布、タクト毛布の3種類があります。
今回は、織毛布の代表であるウール毛布ができるまでを見学させていただきました。
毛布を作る反物は1反40mほど。毛布約20枚分にあたります。
織りあがった反物には、織り工程で着いたホコリや汚れがあり、紡績の際に油を使っているため、その脂分を落とすための洗浄が行われます。
織りあがった反物を糸でつなぎ合わせて、大きな洗浄機へ。
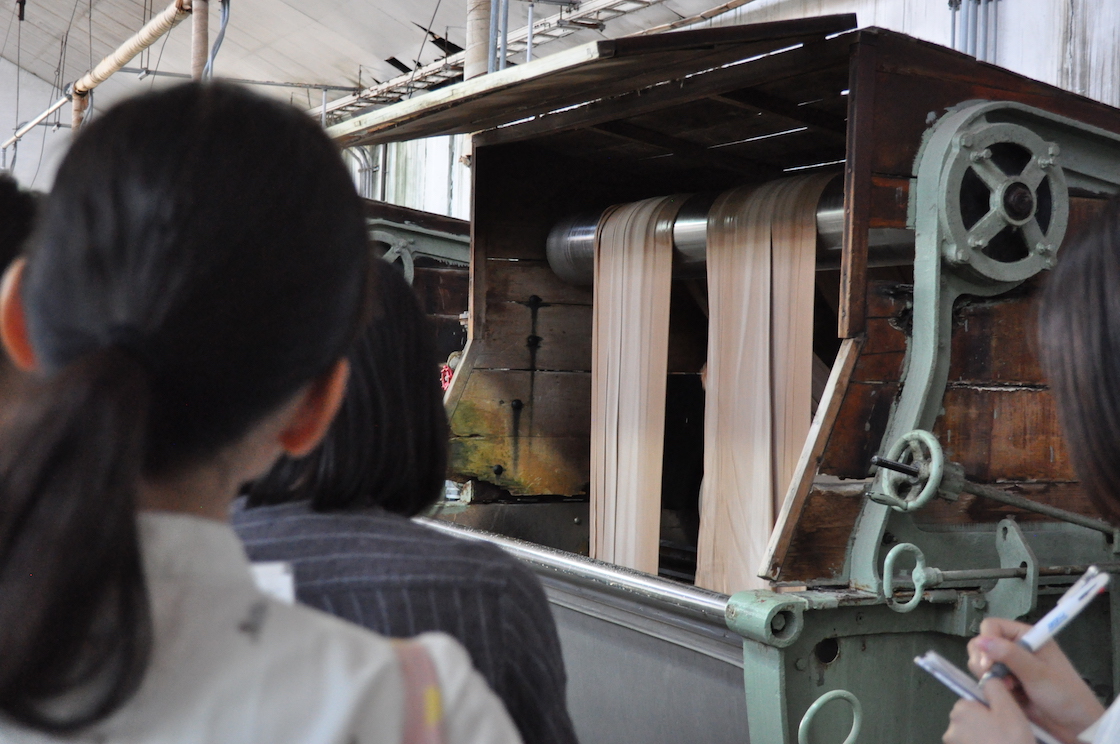
石鹸洗いを5回、水洗いを4回繰り返し、絞るところまでをこの機械で行います。
次は、染めの工程へ。
約100℃の蒸気で加熱。約90分で染めあげたら、大きな脱水機でしぼります。
染色が終わると、次は毛布づくりの要となる起毛工程へ。
ウールの場合は繊維が弱いので、摩擦を抑えて毛羽を取るため、濡れている状態で一度起毛の機械にかけ、乾かした後に残りの仕上げの起毛をかけます。
そうすることで、繊維を傷めることなく満遍なく毛を立たせることができるそう。
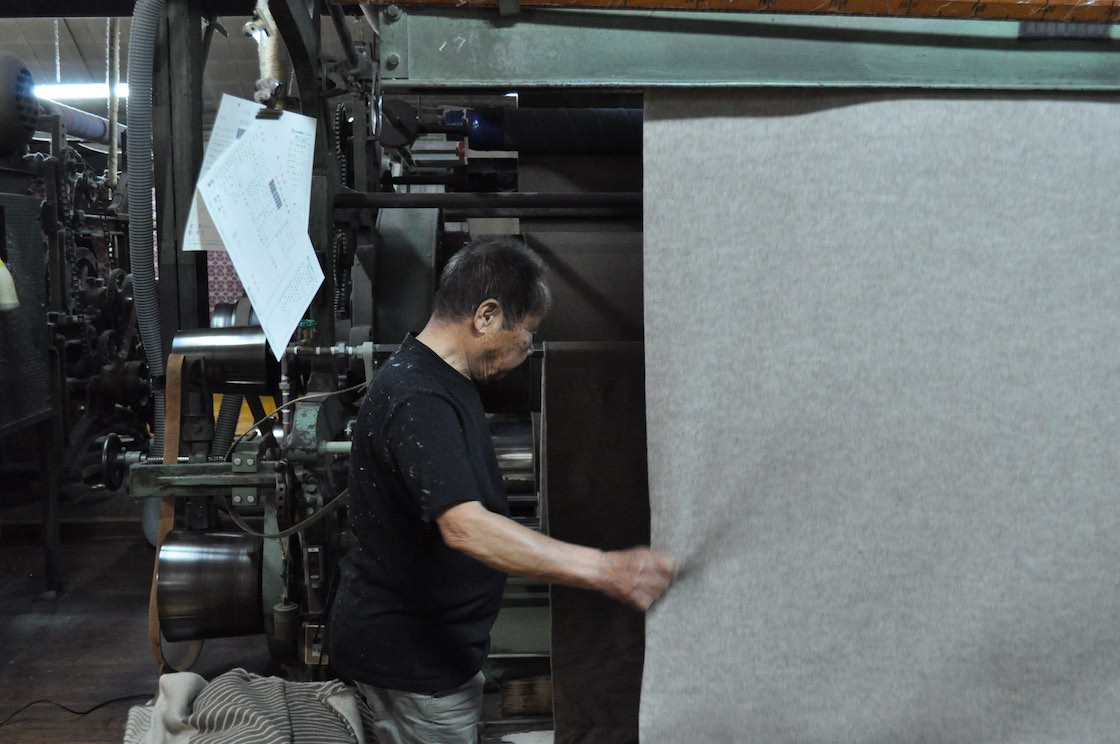
起毛機にはたくさんの針がついたローラーがついていて、繊維を突き刺して持ち上げるようにして毛をだしていきます。ローラーの間を何度も通るうちに繊維が1本1本引き出され、柔らかな毛布らしい手触りが生まれます。
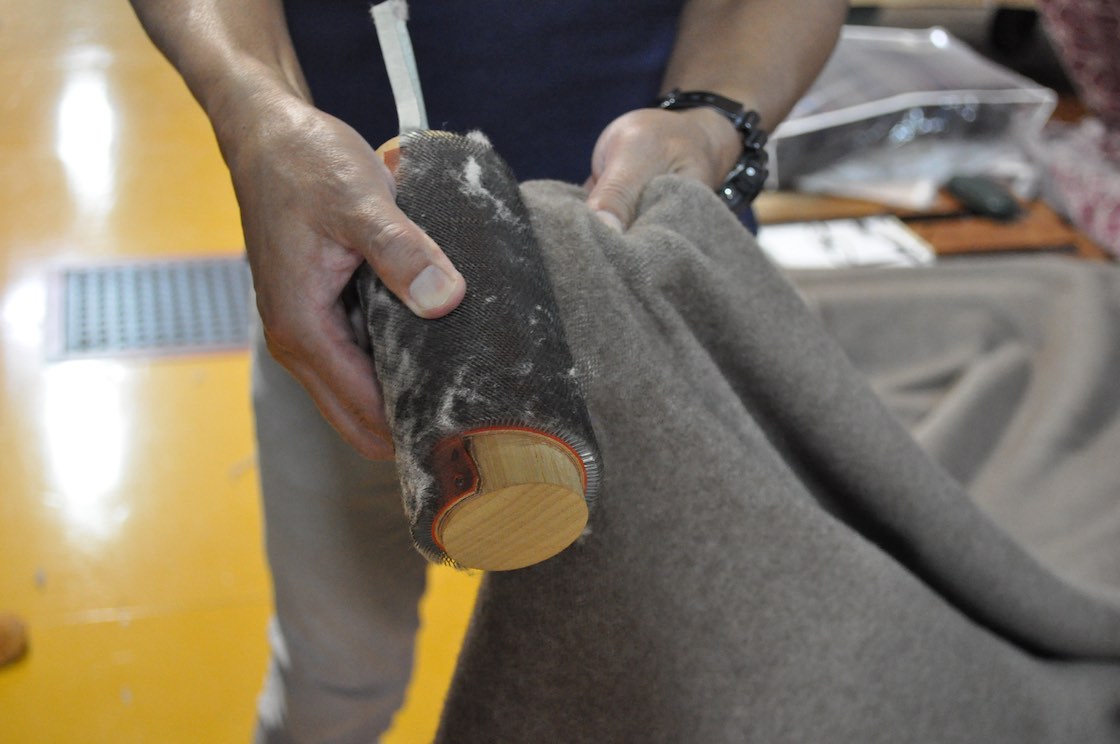
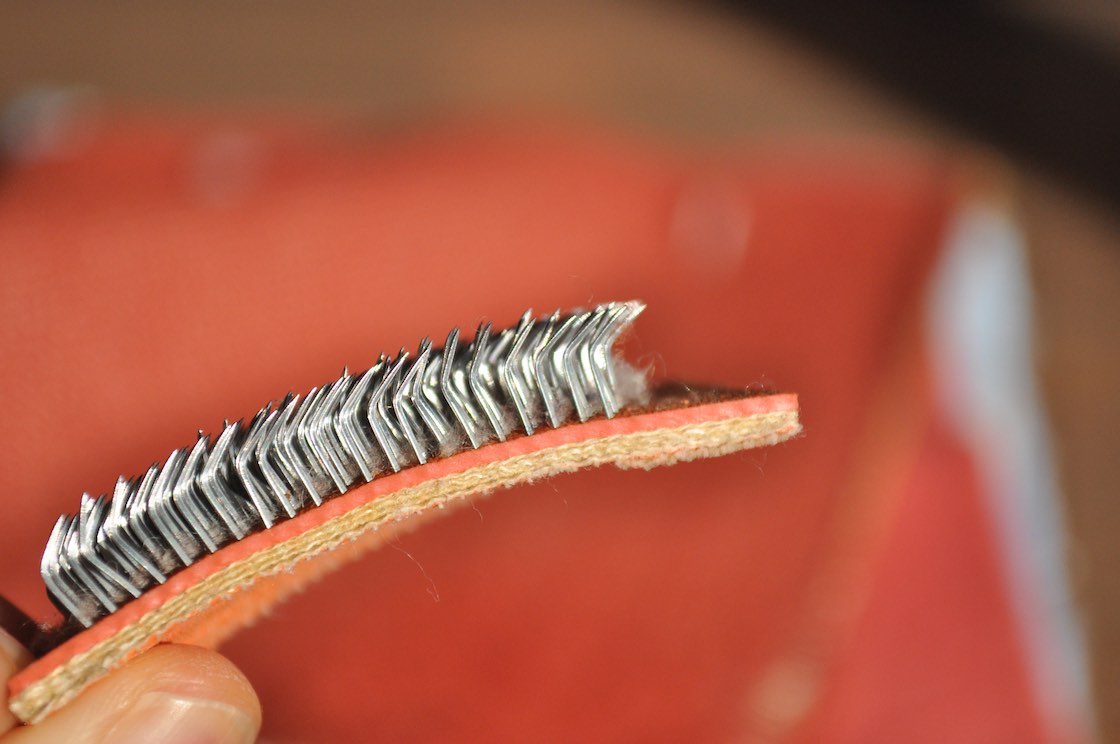
伺って印象的だったのが「起毛というのは、生地の土台を残しつつ、綿(わた)に戻していくということ」という言葉。
綿に戻すという表現に想像が膨らみ、だから毛布ってふわふわなんだ。と改めてものづくりの面白さを感じました。
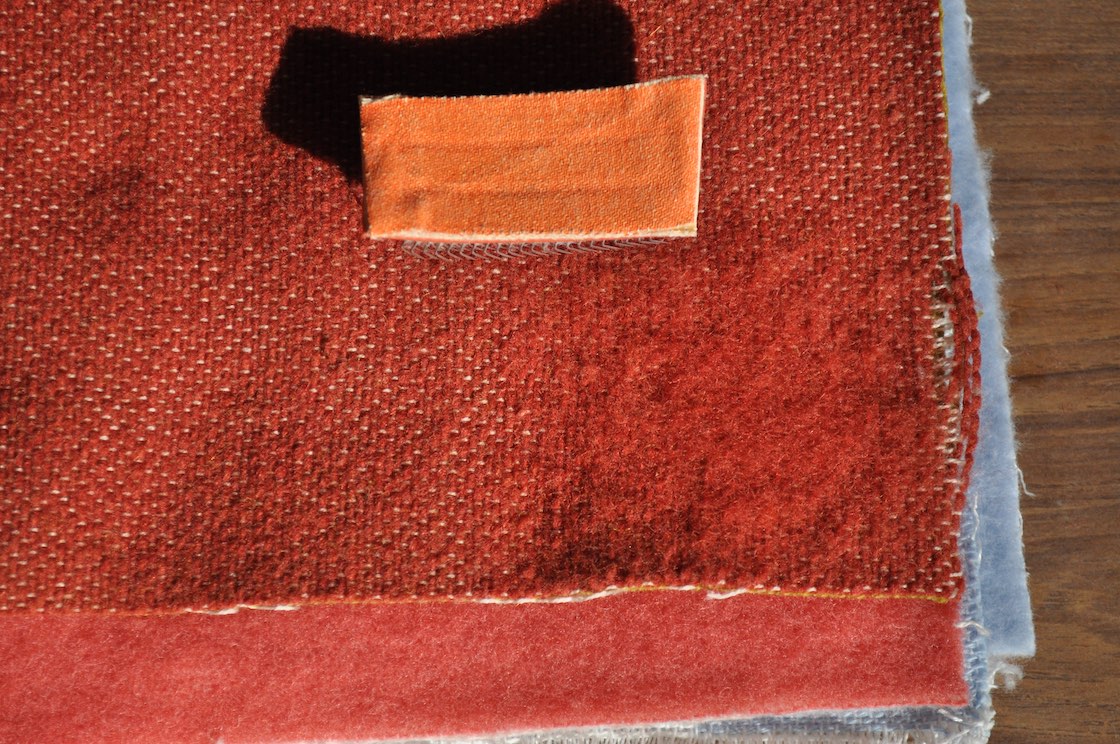
▲起毛する前とした後(右下部分)の違いがわかる見本。これだけ変わるんですね!
起毛は、毛布づくりでは最も重要な工程のひとつで、長年にわたって培われた起毛師さんの熟練とカンによりやわらかな風合いが生み出されています。
「機械で毛羽を出しているけれど、最高の風合いで仕上げるというところは、人の手によって決められているんです」という今井社長の言葉が心に残りました。
その後、仕上げとして起毛した毛の長さを揃えてカットするシャーリングと、毛の縮れに高圧のアイロンをかけて延ばすポリッシャーという処理が行われ、表面に光沢が生まれすべすべの手触りの毛布になっていきます。
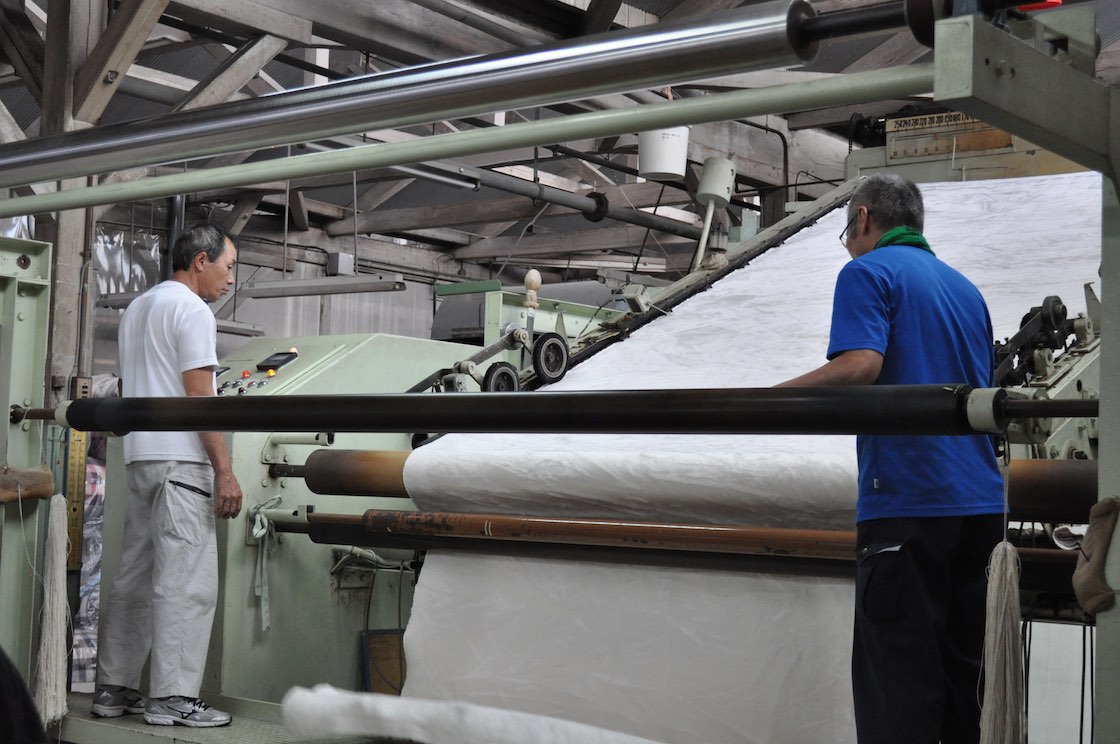
最後の縫製工程では、両方のふちにヘムを縫い付けて裁断し、手作業で幅方向のヘムとタグを縫い付けて完成。
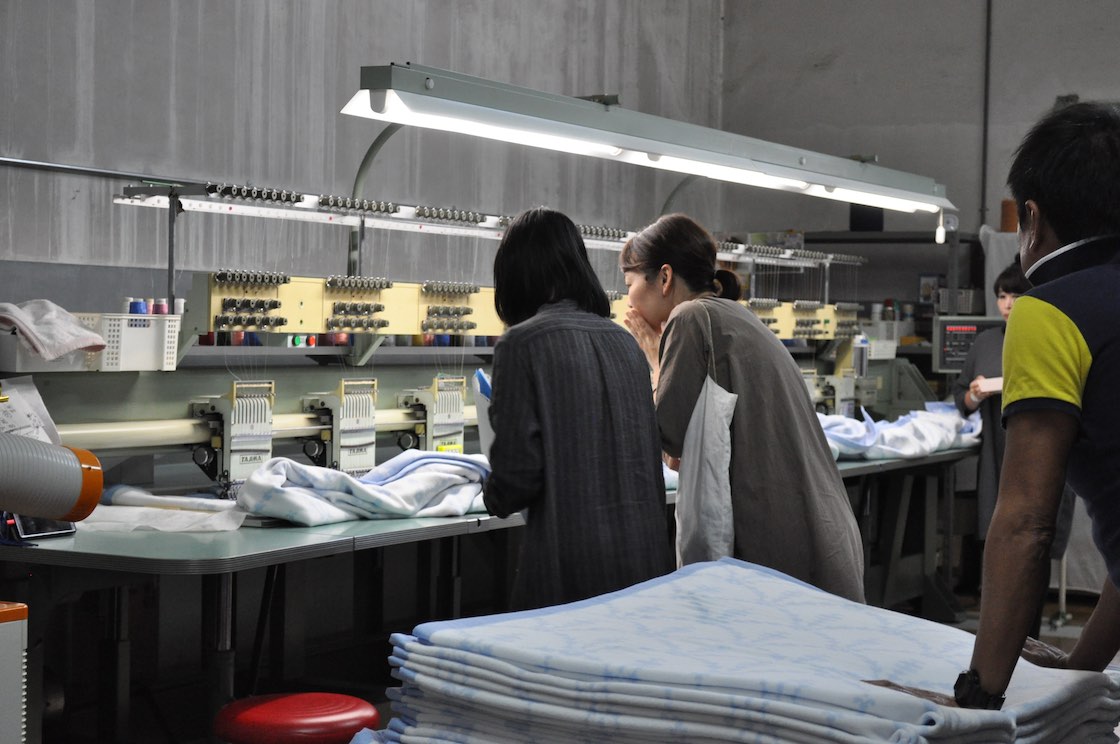
たくさんの大きな機械を通して毛布が完成する傍ら、その工程ごとに毛布の仕上がりを実際に手で触れて確認するということが大切で、手触りのよい毛布を作り上げるためにはたくさんの人の手がかかっているということを感じました。
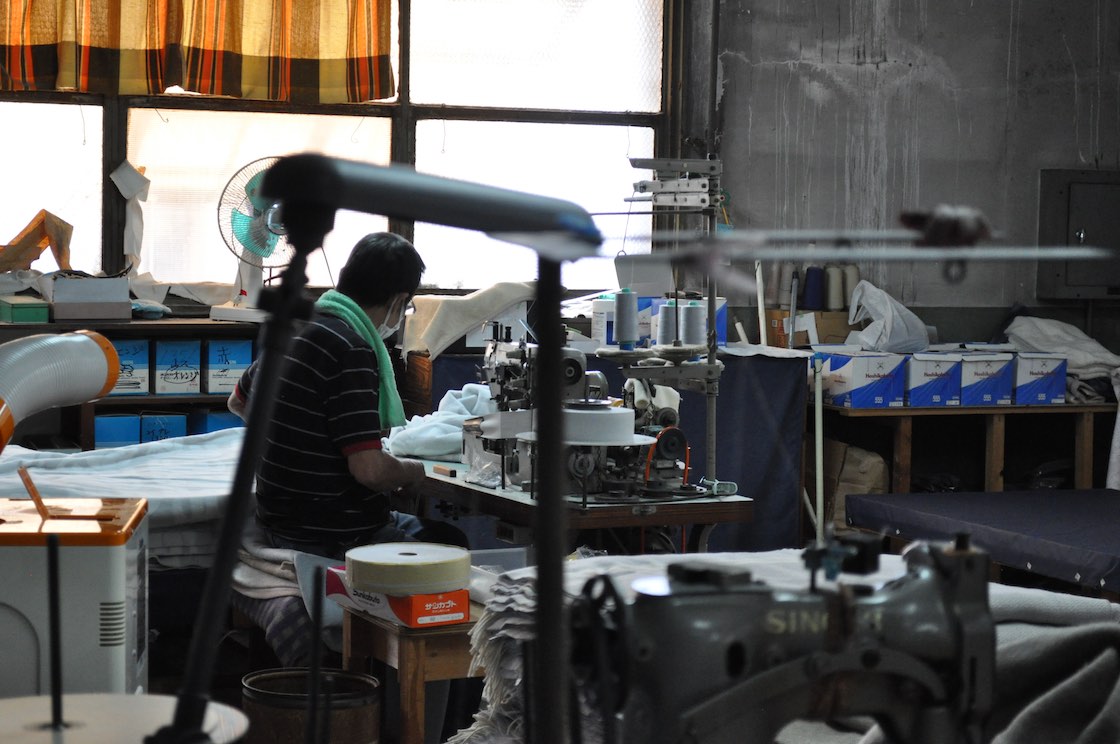
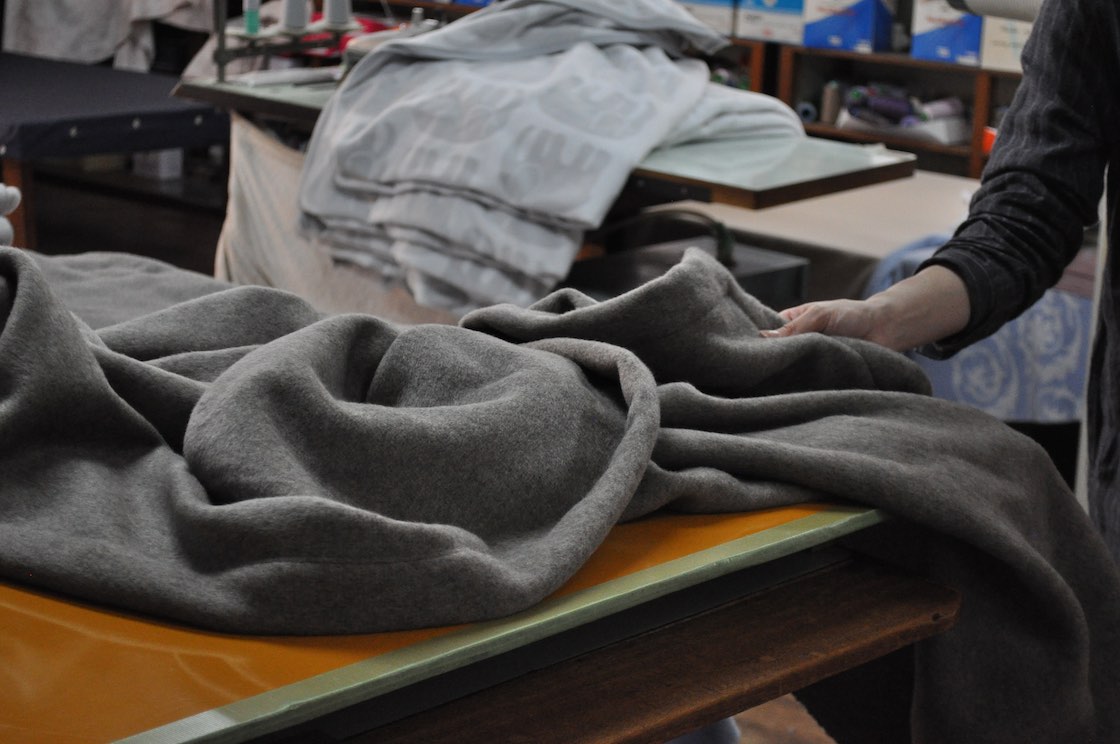
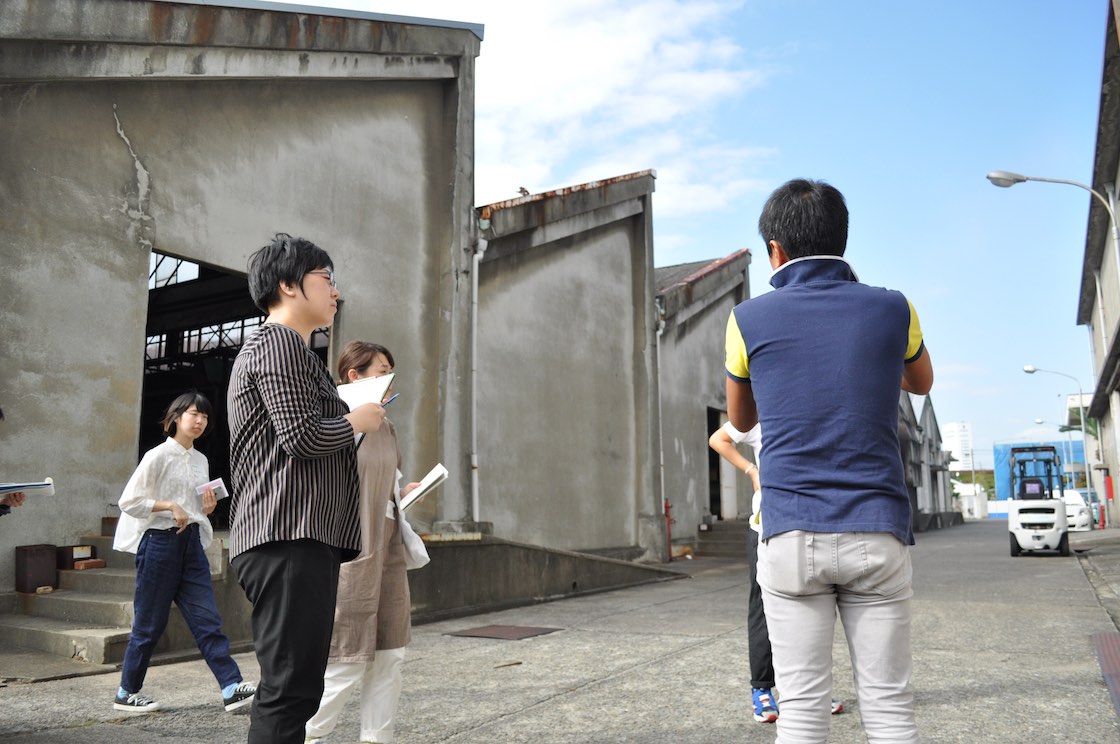
▲ 今新毛織の工場。まるでひとつの町のように広いこの場所で、様々な工程が行われています
全盛期には3000万枚という生産量でしたが、海外から安価な毛布が入ってくるようになり今ではピーク時の5%ほどに減ってしまったとのこと。
毛布ならではのやわらかい肌触りの生地を、毛布としてだけでなく他の製品として生活に取り入れられるのでは…と新しいことにもチャレンジしていきたい。と今井社長。
中川政七商店の「泉大津の2重織毛布」や新商品「泉大津の毛布でつくったかいまきウェア」「泉大津の毛布でつくったルームシューズ」にも、そんな今井社長の熱意が込められています。
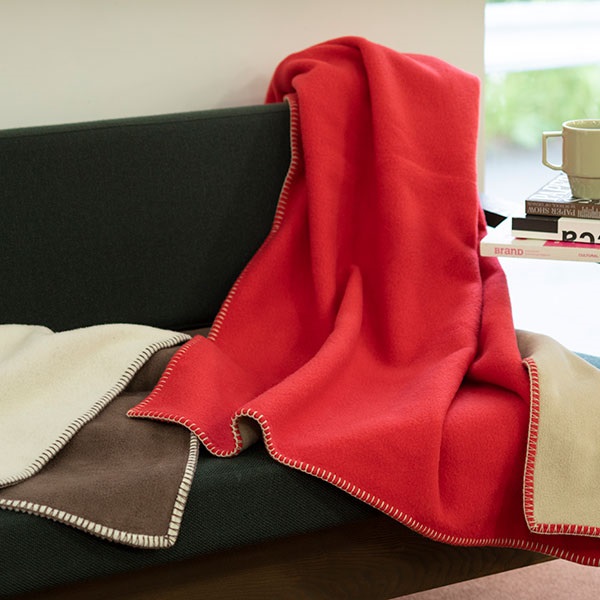
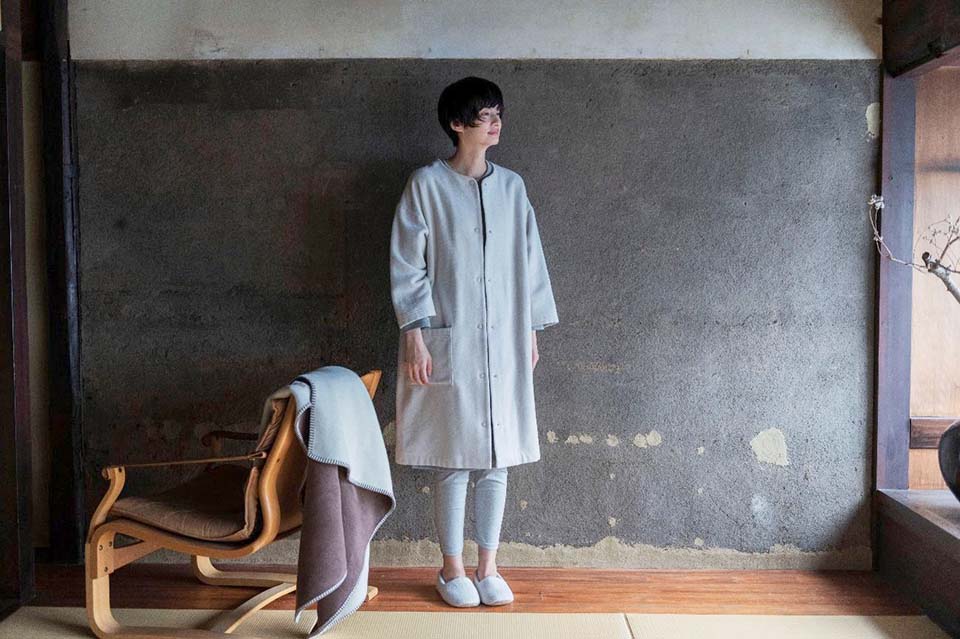
毛布でつくったあたたかくて、肌触りの良いルームウェアは冬の寒さを和らげてくれることまちがいなし。
毛布やさんが作っているからこそ、ふっくら嵩を出す起毛が実現されているということを実際に手に取って感じていただけるように、お店で伝えていきたいと思います!