中川政七商店のものづくり実況レポート。実は日本一の産地、奈良の靴下づくりとは?
エリア
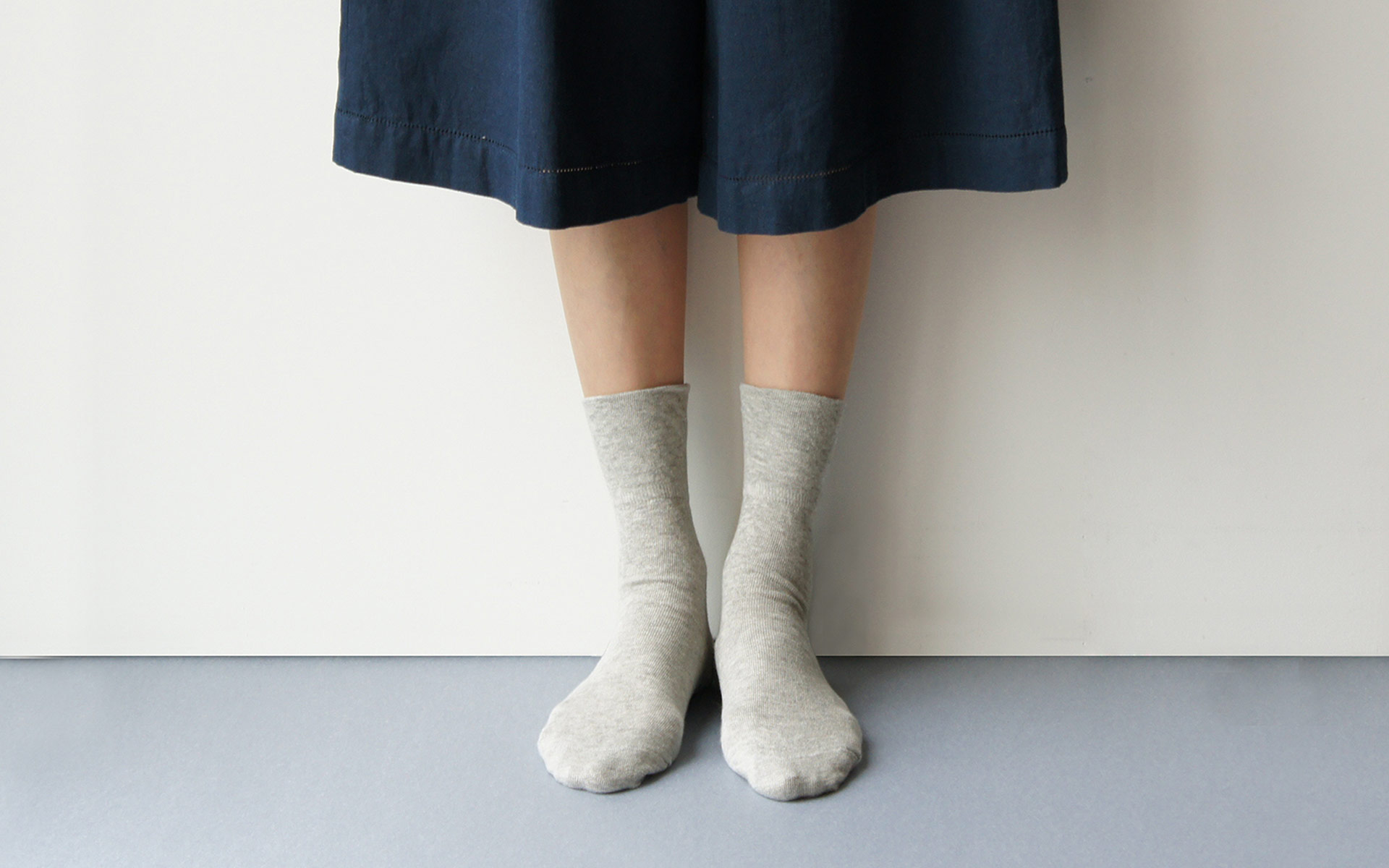
“奈良”と言えば、皆さんは何が思い浮かびますか?
代表的なものは、「鹿」や「大仏」でしょうか。
もしかすると、「中川政七商店」と思ってくださる方もいらっしゃるかもしれませんね!
“奈良”と言えば実は、「靴下」の生産、日本一の産地なんです。
暮らしに欠かせない道具である靴下。
その魅力や仕組みについて学ぶべく、私たちスタッフは「さんち修学旅行」と題して今年1月に奈良の靴下工場を訪ねました。今日はその様子をお届けします。
靴下メーカーさん2社の工場見学
修学旅行にご協力いただいたのは2つのメーカーさん。
日本市博多デイトス店の白井から
まずは1軒目の「瀬川靴下株式会社」さんについてお届けします。
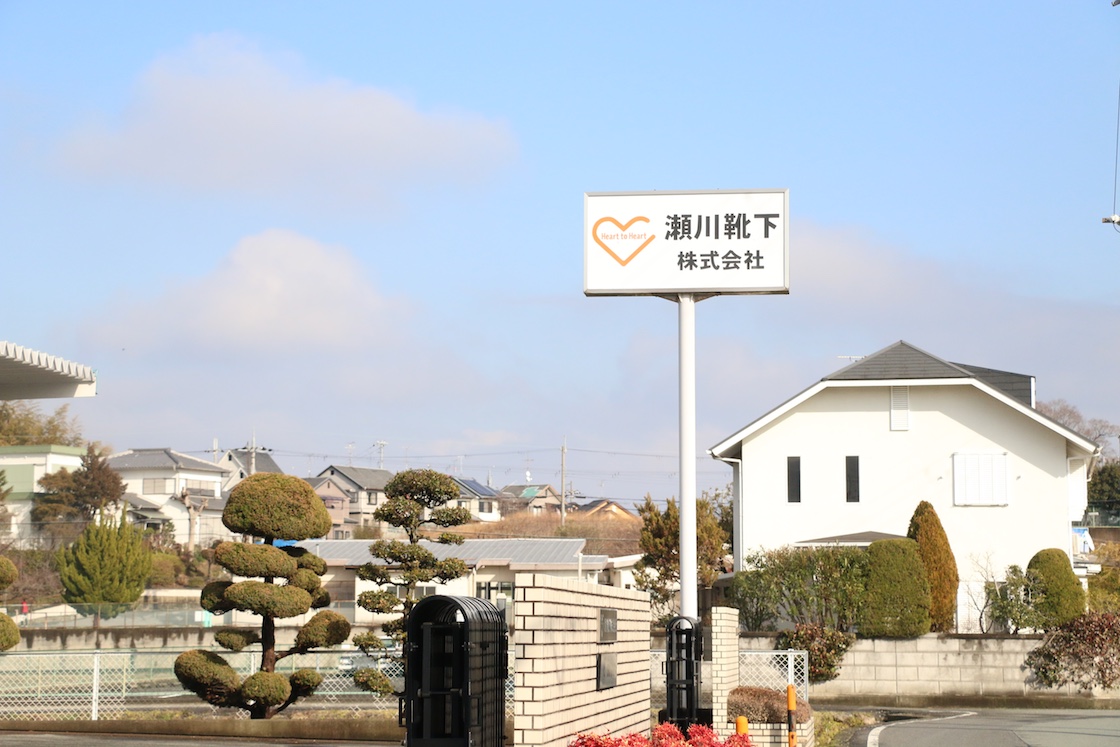
瀬川靴下株式会社さんは、「鹿の家族の靴下」や靴下ブランド2&9(ニトキュー)の「しめつけないくつした」を作ってくださっているメーカーさんです。
工場の中では靴下のサンプルを作るところから商品として出荷するまでの
ほぼすべての工程が行われています。
一連の工程を見学させていただきましたのでご紹介します!
靴下ができるまで
まずは靴下の設計図づくりから。
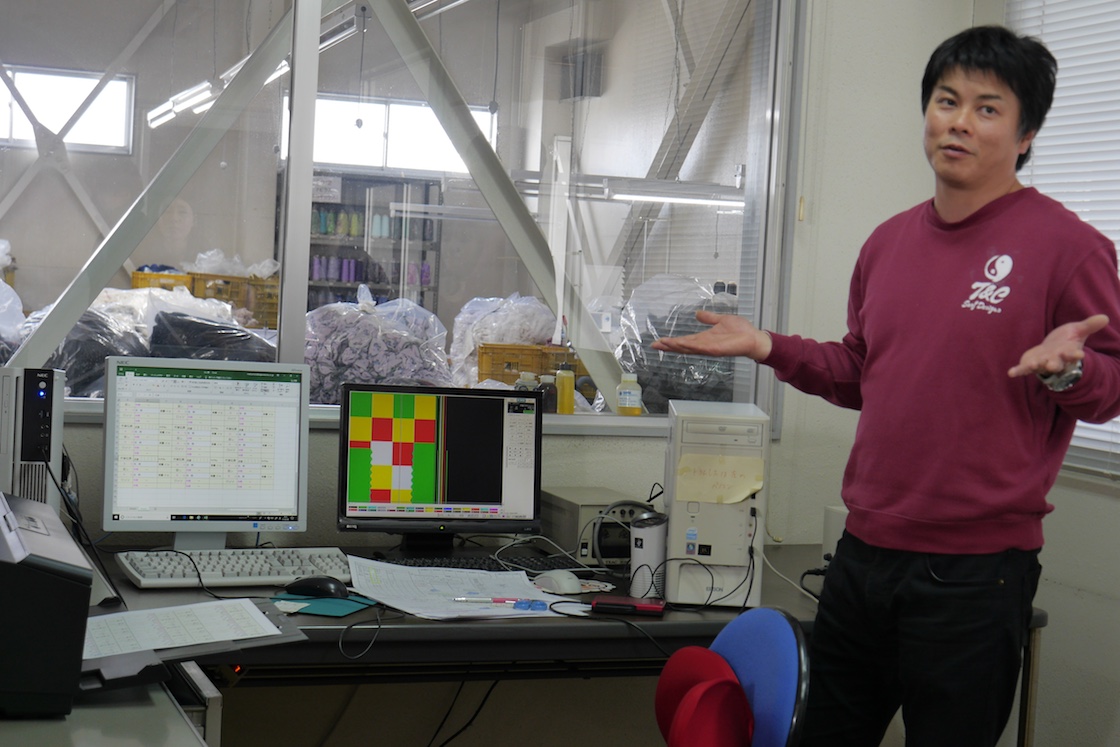
靴下を編むのは機械なので、靴下の設計図もデータ化されています。デザイナーさんが考えたデザインを、ドットで表現していきます。
設計図ができたら、次は糸の調達です。
靴下によく使う綿の糸は伸縮性がないため、綿の糸だけで靴下にしても足にフィットしません。綿の糸と一緒に伸縮性のある糸を使うことで、初めて伸縮性のある靴下ができます。
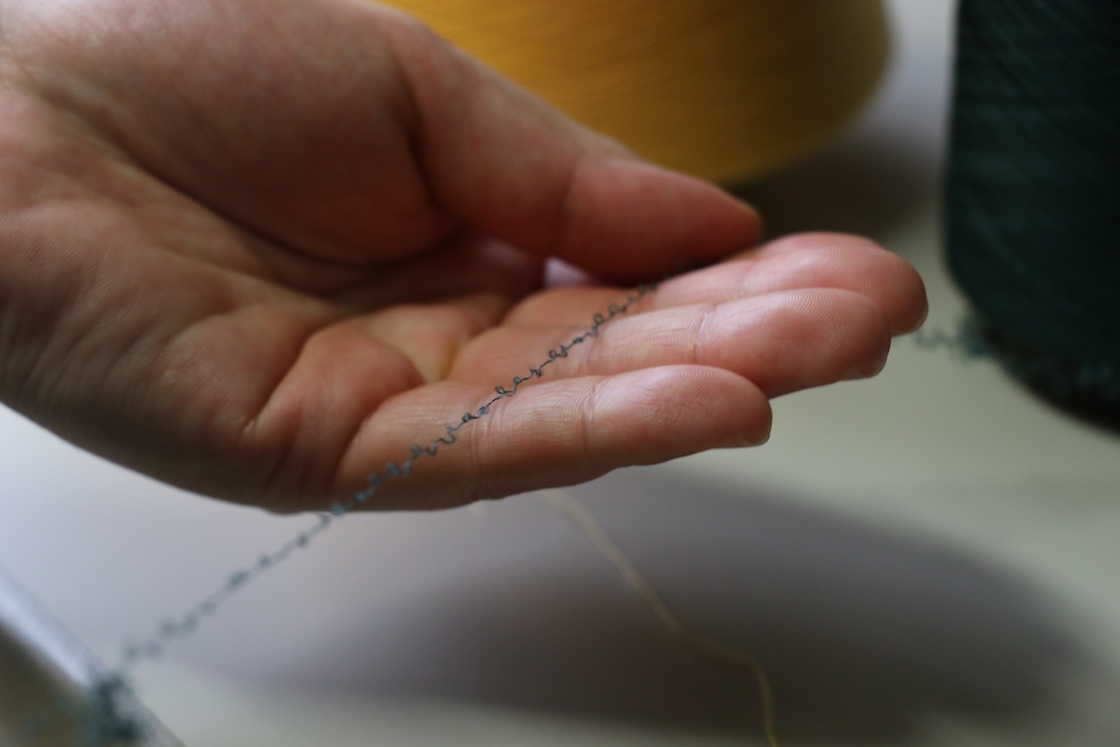
ちなみに2&9のしめつけないくつしたは、従来の靴下よりも伸縮性の弱い糸を使用することで、しめつけにくいように仕立て上げています。そのため足をやさしく包み込むような履き心地になりました。
次にどの機械でどれだけの靴下をどれくらいの期間でを編むのかを決める「配台」です。この配台がとても重要だそう!
たくさんの事前準備を経て、ここからやっと「編み立て」の工程に入ります。
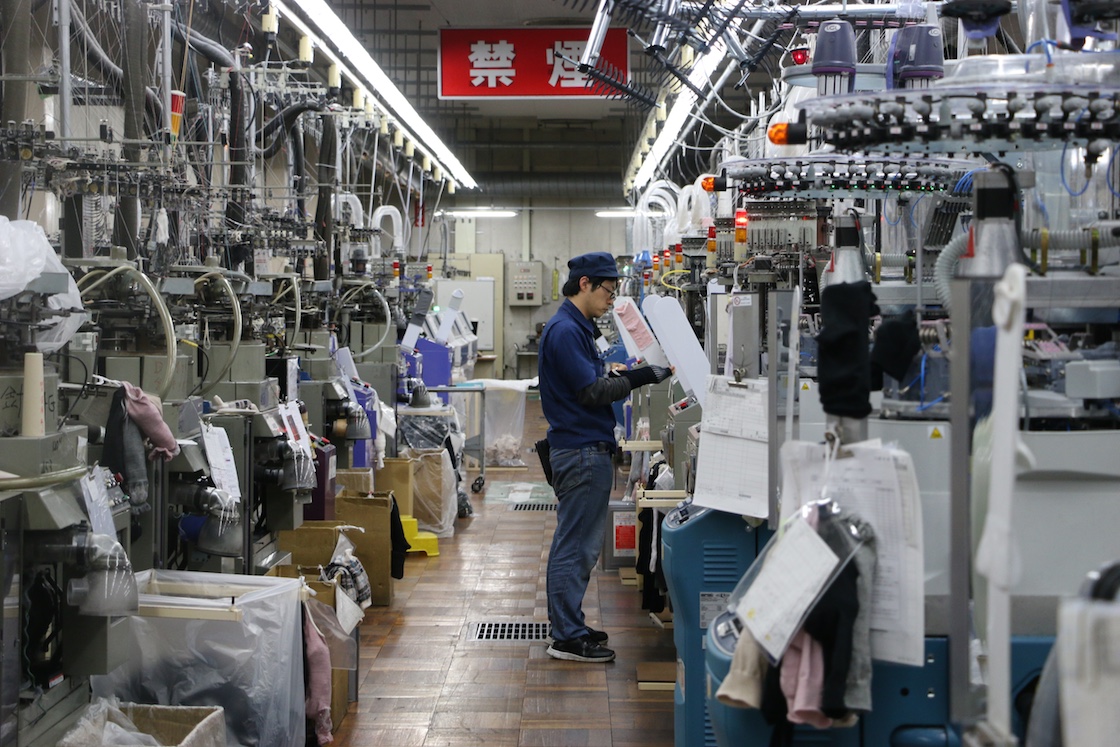
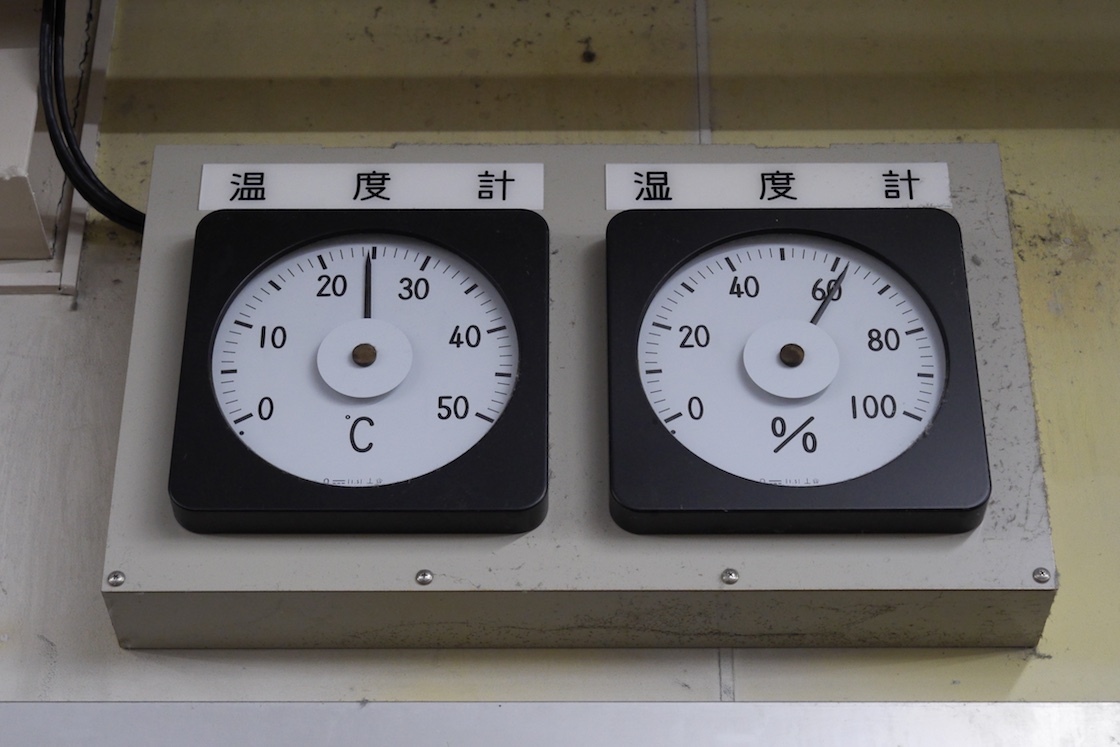
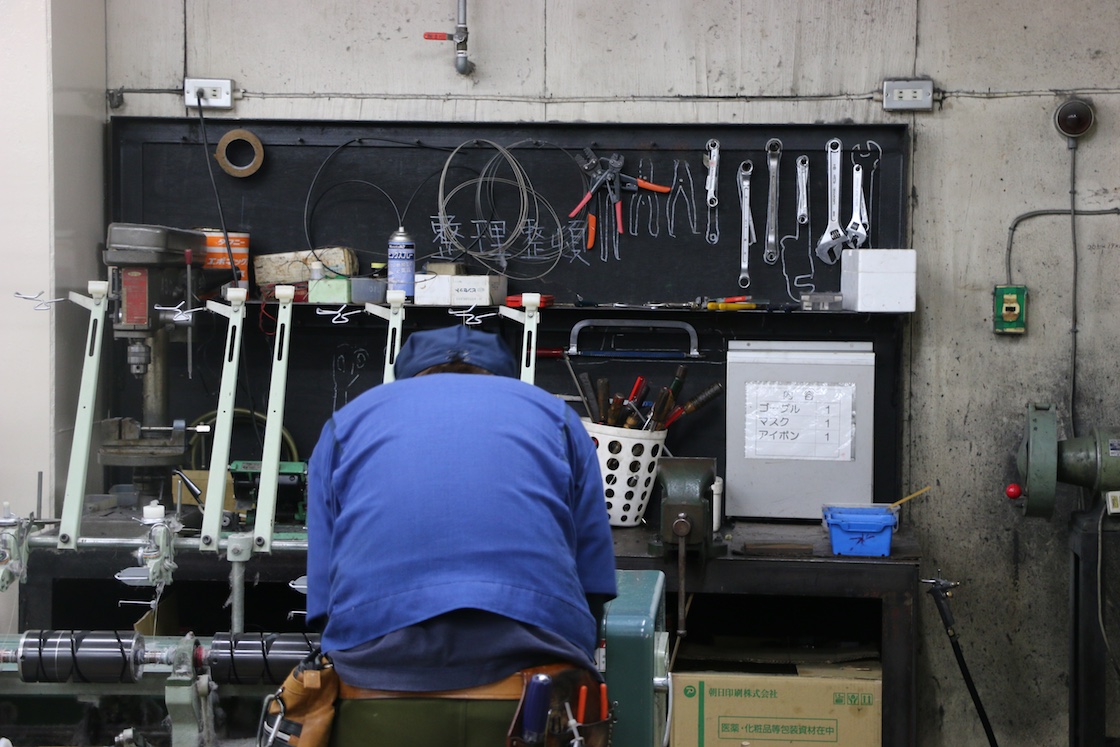
工場内では何台もの機械が靴下を編み立てており、機械の音に満ち溢れていました。
編み立てた靴下は、まだ完成ではありません。この「編み立て」の工程では筒状の編み物を作っています。
編み立ての終わった靴下は、靴下を裏に返す「返し」を行い、つま先の部分を縫製する「ロッソ」という工程にうつります。
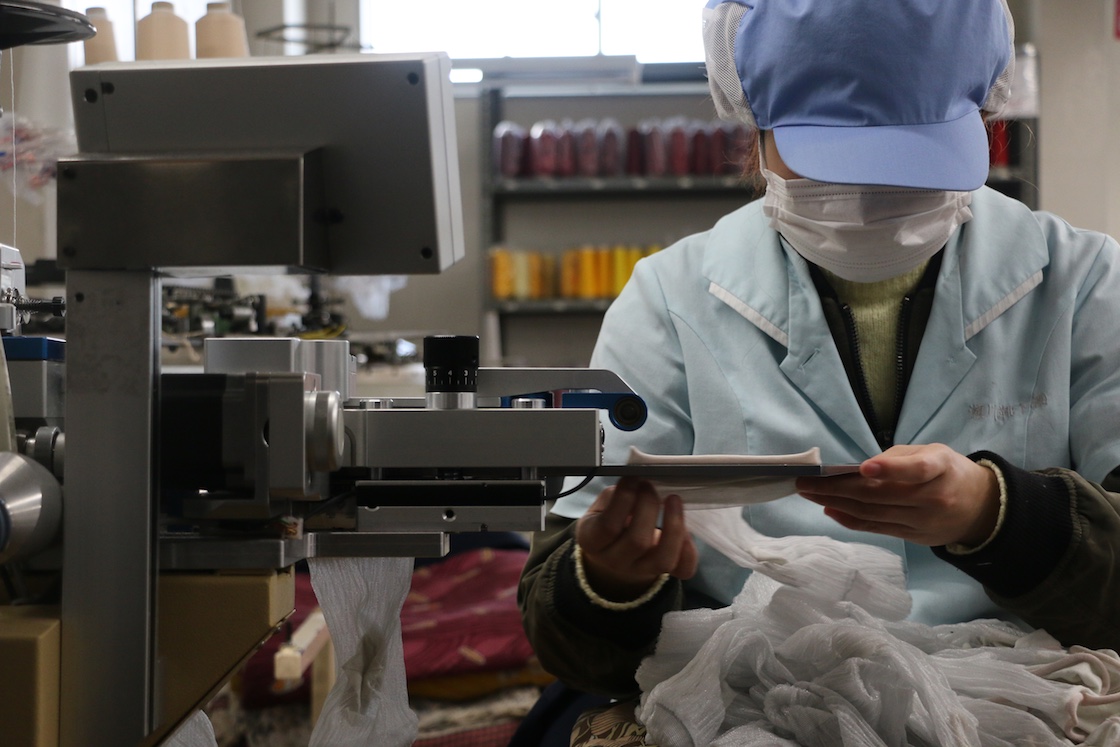
「ロッソ」という言葉はイタリア語だそうです。
つま先を縫う機械を作っているメーカーさんがイタリアの「ロッソ社」というそうで、その会社の名前を「先縫いをする」という意味で使うのが時代の流れとともに靴下業界で定着していったそう。
また、奈良の農家にはそれぞれの家庭にロッソの機械があり、農業の合間に副業として納屋の中でロッソをしていたそうです。
ロッソの工程後、やっとよく見る靴下の形になりました。
ここから、靴下がお店に並ぶための準備に入ります。
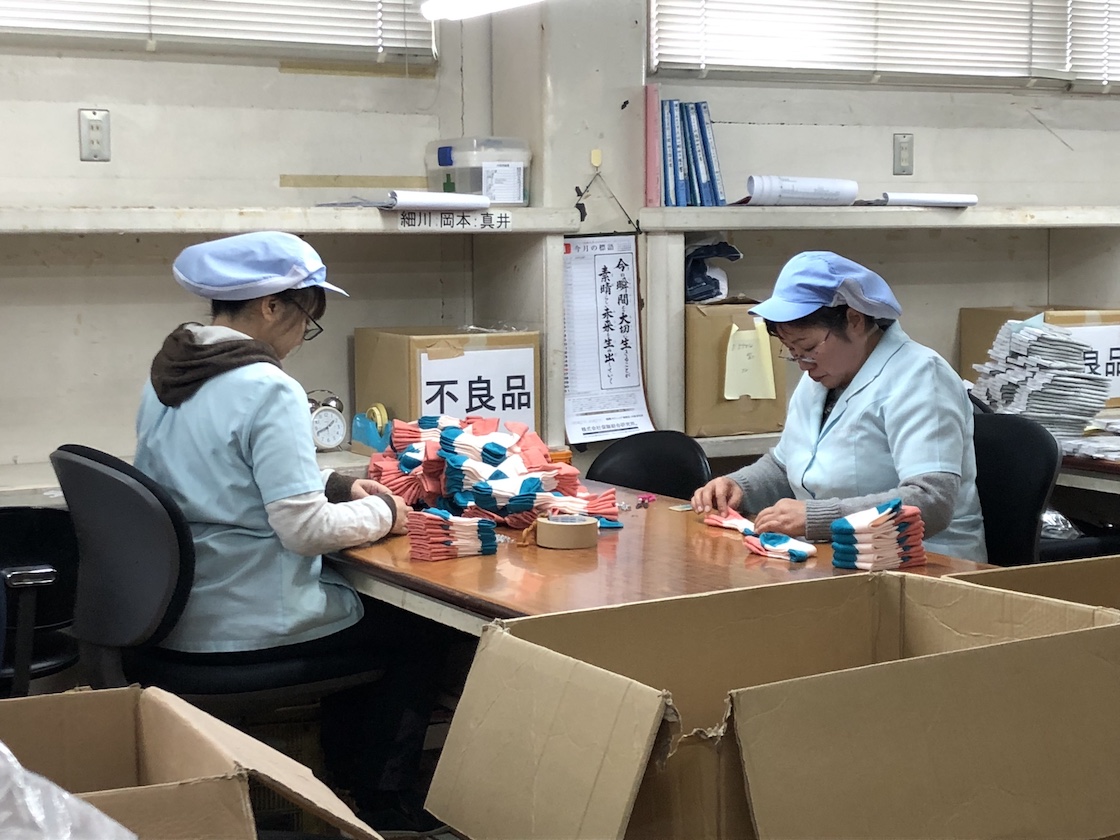
ひとの手で靴下を表に返し傷がないか検品(「傷見」といいます)したあと、蒸気を当てて形を整えるセットをし、2枚を1組にまとめる「ペアリング」という工程を行っています。
その後、販売に欠かせない商品のタグやシールなどをつける「装飾加工」とその検品、最後にお客さまが安心して靴下を履けるようにするべく、「検針」の工程にうつります。
検針の機械は、1日に5回も正常に動くか点検をしているそう!
検針が終わった靴下は、前工程までの作業場とはパーテーションで区切られて、品質管理上戻ることのないようになっています。
そして、箱詰めされて出荷されていきます。
一連の工程を見学させていただく中で、作り手のみなさんの職人技と靴下をつくる環境への気配りに終始圧倒されました。
瀬川靴下さんで学んだことを早くお店に持って帰りたい、お客様に伝えたい!と一同大興奮ですが、まだまだ靴下の勉強は続きます。
ぬげにくいくつしたの秘密
2軒目は「株式会社キタイ」さんへ伺いました。
ここからは中川政七商店 博多アミュプラザ店の松本がお届けします。
今回は店舗でも毎年大人気、春の販売をスタッフも待っている「ぬげにくいくつした」や「アームカバー」などの製造工程を実際に見て学びました。
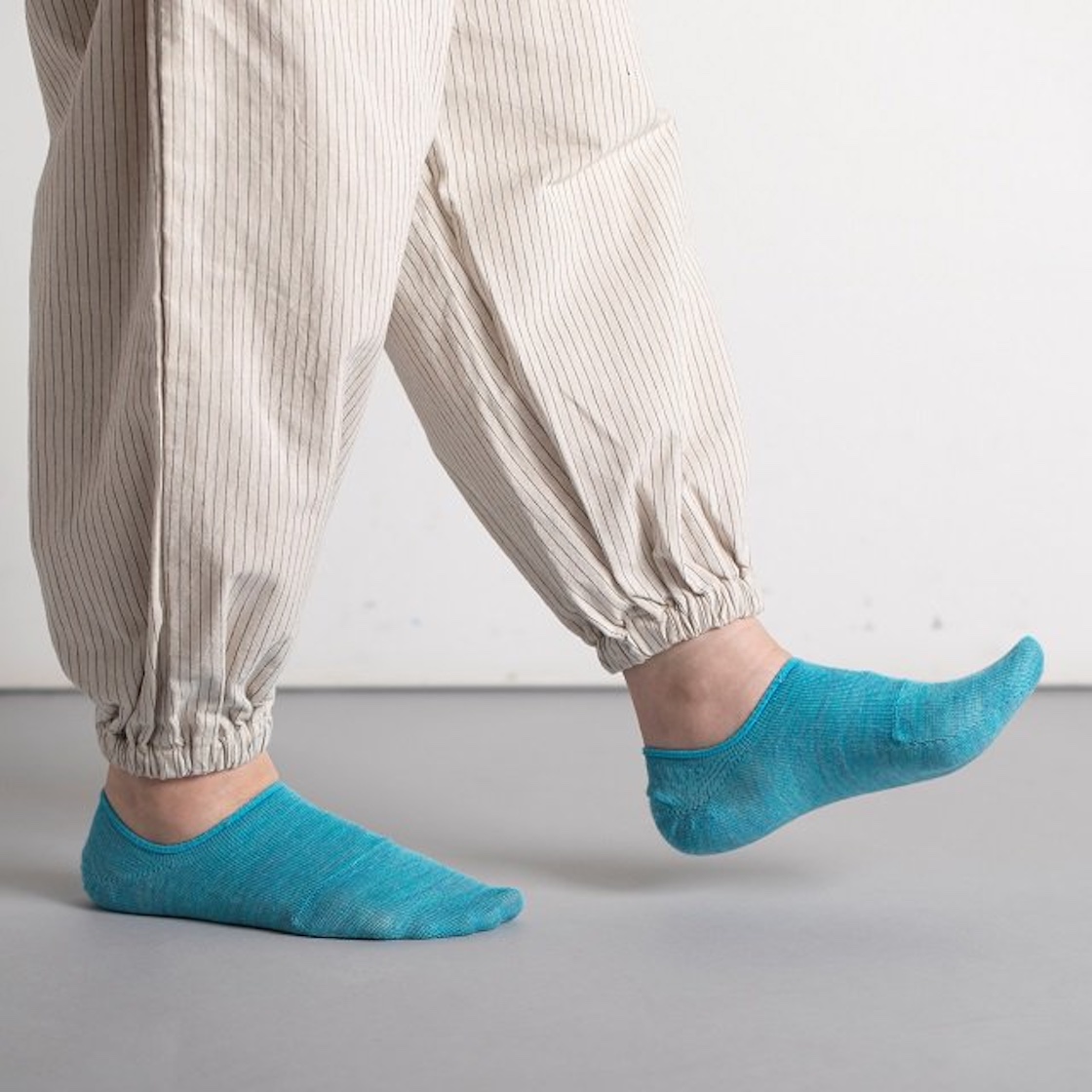
ぬげにくいくつしたは全体の7割が「立体成型」の技術を用いて編まれているので、足の形にフィットします。
立体成型の技術は通常だと正回転のみで編むところを、正回転→逆回転→正回転と編み方を切り替えて繰り返すことでギャザーのような線がたくさん靴下に入り、立体的な形になるそうです。
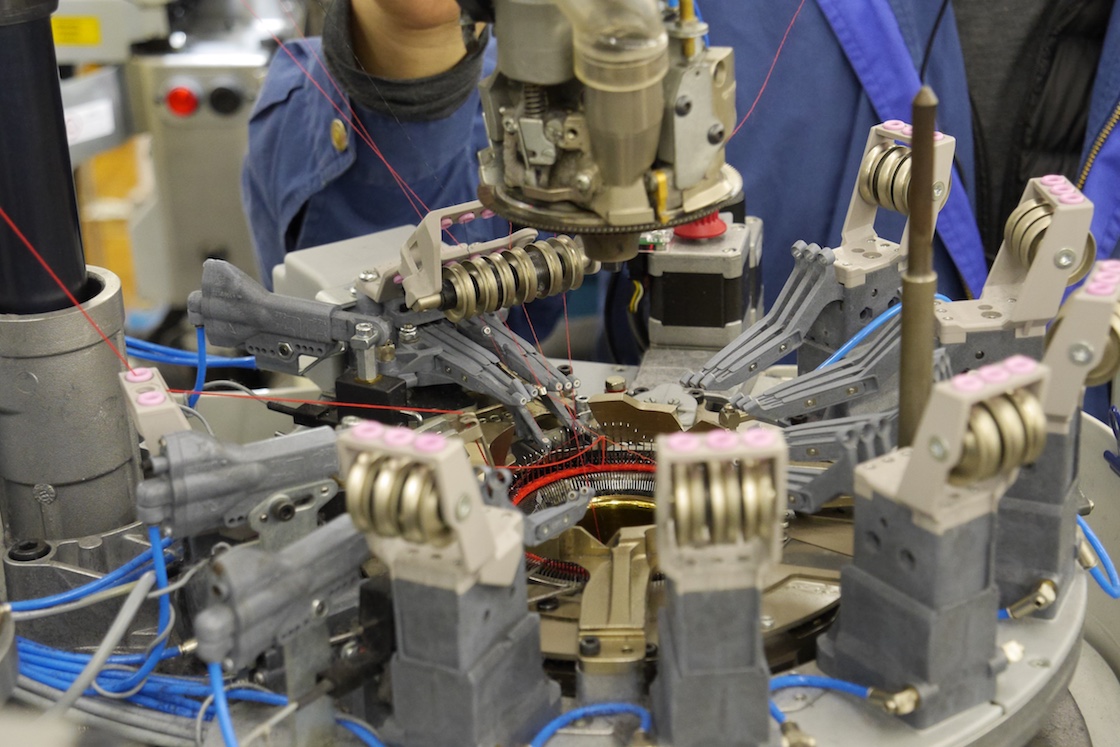
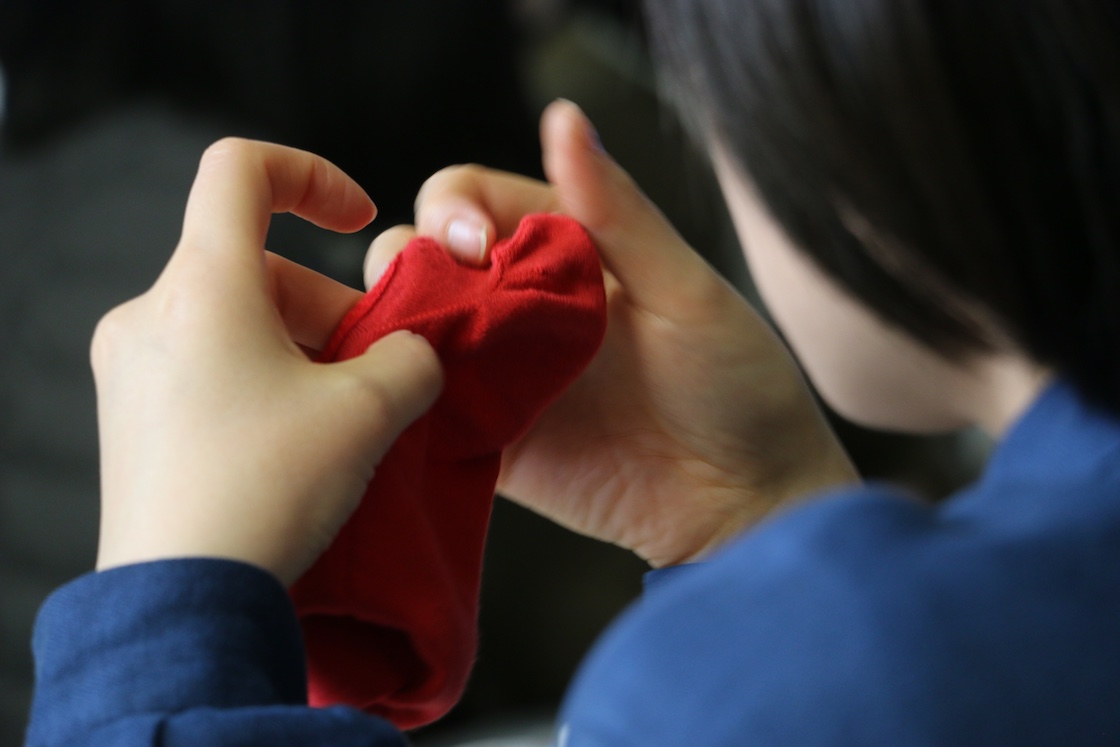
複雑な編み方のため、完成するまでの時間は1足あたりなんと10~15分。
そのため、大量生産はできませんが、この技術のおかげでストレスなく靴下を履くことができます。
また、沢山ある作業工程の中でも特に心打たれたのは、靴下の足裏に入れるロゴの転写作業です。
「2&9」のくつしたの足裏に、さりげなくプリントされているロゴマーク。
実はこちら、人の手で一点一点、転写されているのです。
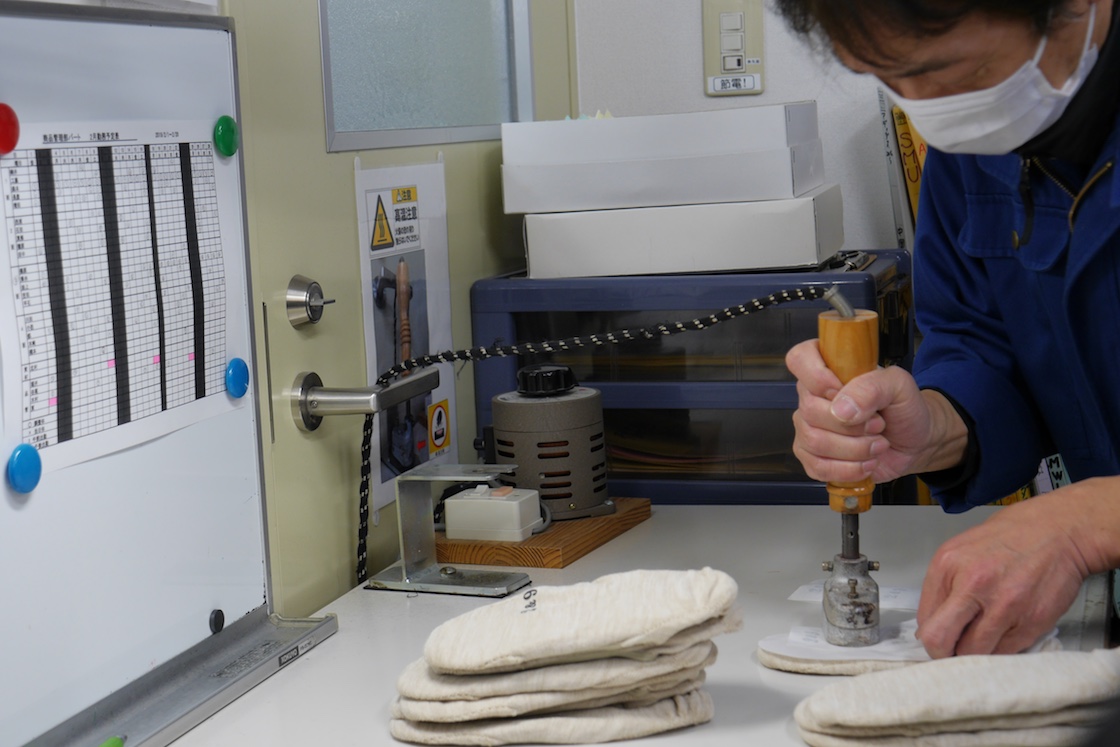
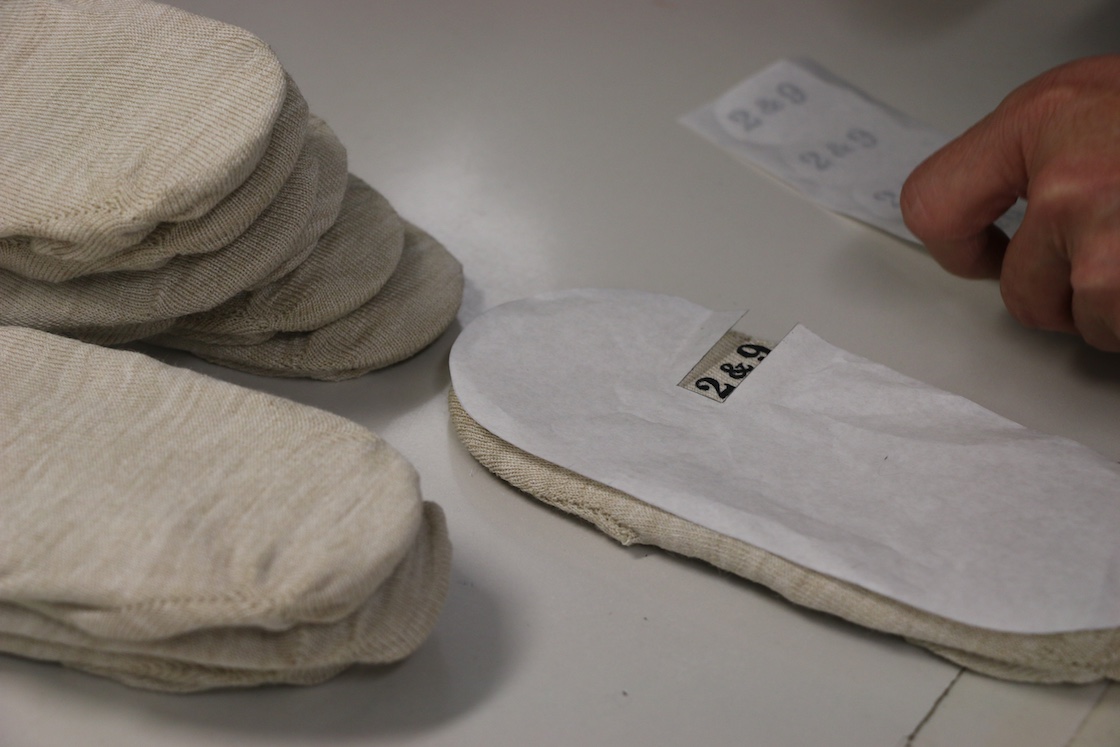
きれいに転写するには細かな技術が必要で、この作業ができる方は数名の熟練の方に限られているそうです。
すこしの段差や凹凸でロゴがゆがんだり、ロゴの位置がずれてしまわないよう、靴下の内側にセットした台紙を一旦はずし、転写する場所を平たくしてから作業開始。
力が均等にかかるようできるだけ薄い紙で作ったガイドを載せ、熱したコテで転写シートを適切な力加減で押さえます。
力が強すぎればロゴがにじみ、弱ければかすれてしまう繊細な作業。
靴下を履いてしまうと見えなくなってしまうポイントにも、工夫と手間が詰まっていることを実際に目で感じ、いつも履いていた靴下により愛着が湧きました。
また、靴下を編む工程だけでなく不良品がないかをチェックする検品にもとてもこだわりを感じました。
破れ・ほつれがないかなど、なんと27項目にも及ぶチェック項目を人の手と目で丁寧に全数検品をされていました。
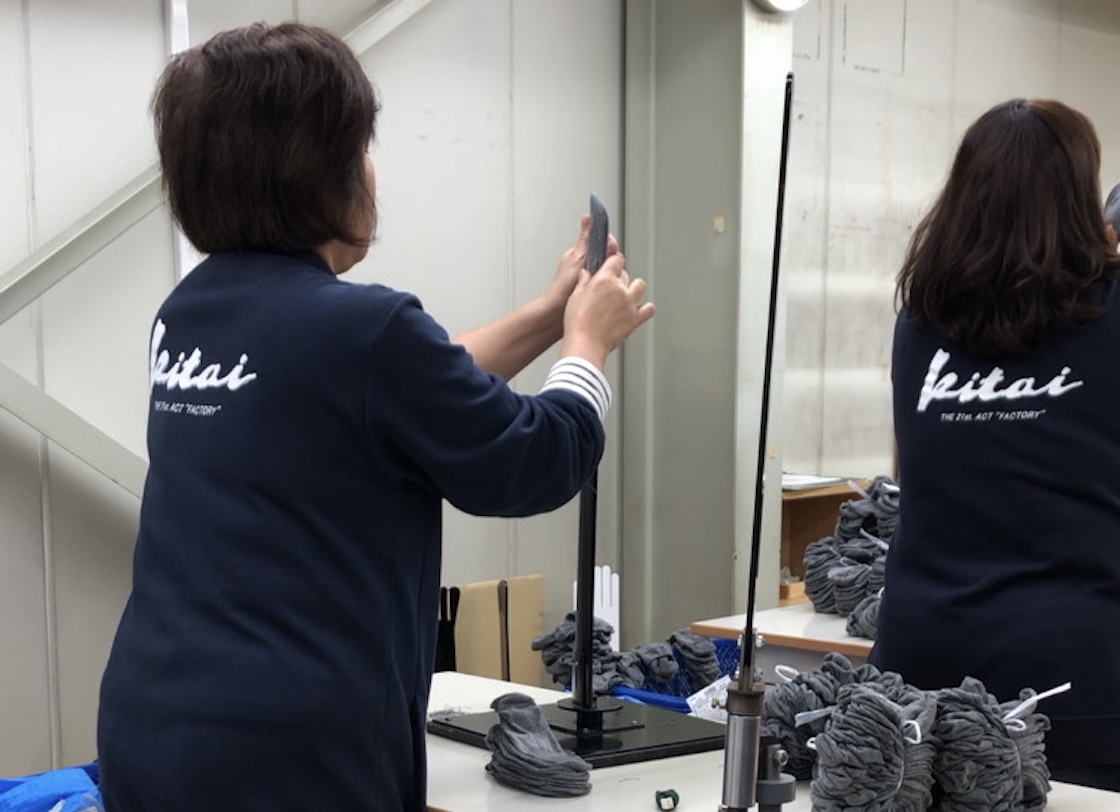
機械で単純に作られている訳ではなく、多くの人の手を通して店頭へ並ぶのだと改めて感じ、気が引き締まる思いでした。今年も実際に店頭に並ぶまであと少し…!とても待ち遠しいです。
今回の旅を通じて感じたこと
今回、実際に靴下が出来上がっていくようすや、そこに関わる作り手さん、機械のようすを目の当たりにして、メーカーさんをより身近に感じ、そこに関わるものやことを大事にしたいという気持ちが湧きました。
特に心に残ったのは株式会社キタイさんの喜多専務が仰っていた言葉です。
「作り手として、靴下を消耗品と思わないこと」
日本一の靴下産地奈良の会社として、わたしたちも暮らしの大事な道具である靴下を消耗品とは思わずに、より長く愛着を持って使うことのできる方法を提案していこう!と思いました。
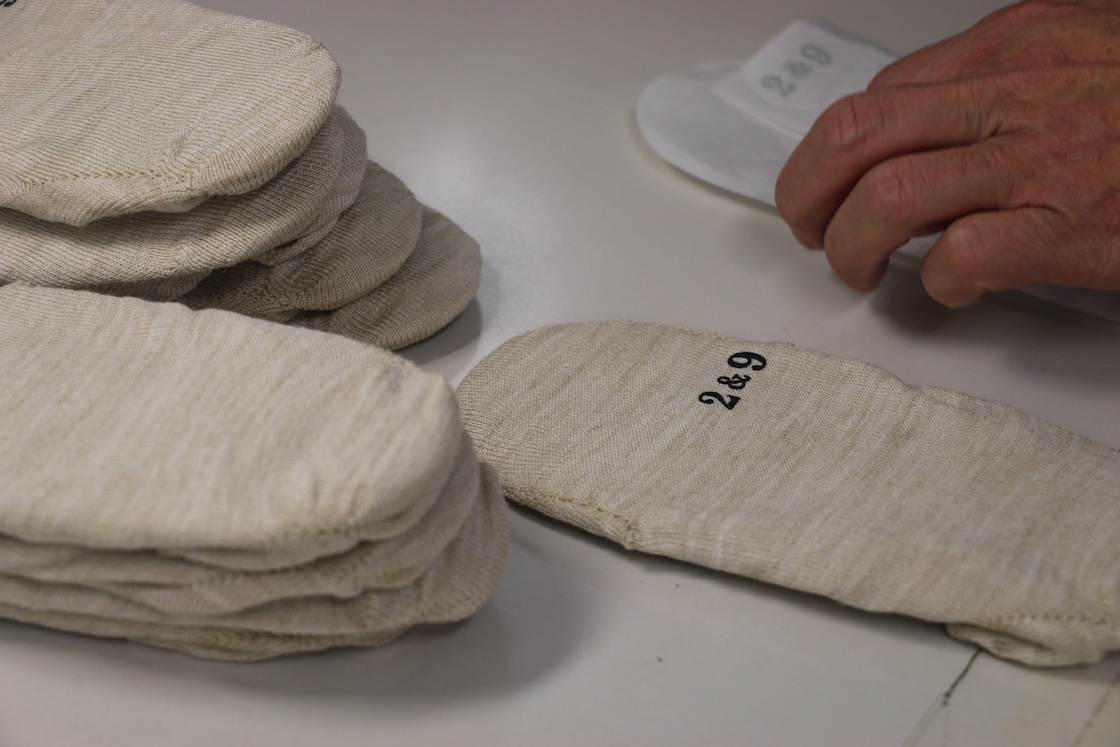
全国のお店で、奈良で作った靴下をみなさんにお届けしています。
ぜひお近くのお店で、スタッフにも尋ねてみてくださいね!
<関連商品>
しめつけないくつしたクルー
しめつけないくつした綿麻クルー
ぬげにくいくつした2フットカバーDip
ぬげにくいくつした2ショート 5本指