この時期、足元のあたために欠かせない靴下。こんなに身近なアイテムですが、どのように作られているかご存知ですか?
洋服はなんとなく想像できますが、こんな筒状の編み物、一体どうやって作られているのでしょう?
謎を探るべく、日本一の靴下生産量を誇る奈良県にある、「御宮知靴下(おんぐうちくつした)」さんにお邪魔しました。
まるで木造校舎のような靴下工場
ガチャンガチャンガチャンガチャンガチャン。
すりガラスの扉をガラリと引くと、飛び込んできたのはけたたましい機械音。
ザ・日本家屋の外観から壁一枚を挟んで、中には人の背丈を越える不思議な形の機械がずらりと並んでいます。
ここは奈良県・斑鳩町の「御宮知靴下」さんの工場。法隆寺にも近く、田んぼと民家が広がる住宅街に、民家にしか見えない外観のその工場はあります。
「今稼働させているのは14台です。フル稼働させたら1日で1500足は編めると思います」
案内くださったのは工場長の山下さん。受注した商品の設計から機械の管理まで技術面を全て任されている、この道50年の大ベテランです。
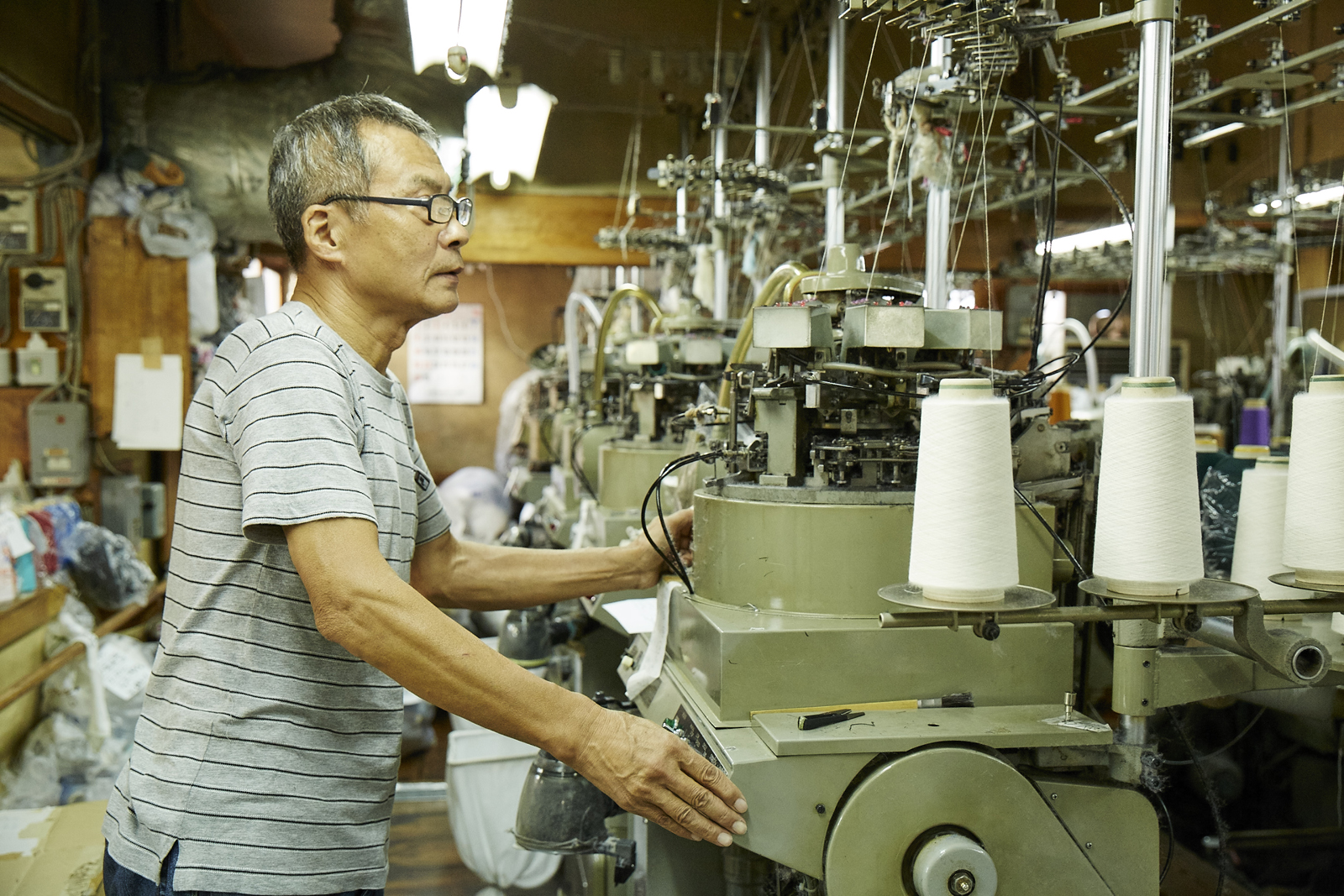
実はこの20分ほど前。お通しいただいた応接室で山下さん、三代目社長の御宮知さんのお二人から普段のものづくりのお話を伺っていました。しかし…
「シングルシリンダーとダブルシリンダーというのがありまして、シングルは履き口が袋状(二重)になります。ダブルの場合はそこがシングルになるんですよ」
「双糸(そうし)は単糸(たんし)を撚ったものです。これで強度が増すんです。その分糸が太くなりますが」
「32単糸(サンニたんし)みたいな糸で作ったらもっと楽ですねんけど」
次々に飛び交う専門用語に、早速頭の中がいっぱいになってきました。
お二人の頭の中にしっかり描かれているイメージが、私には全く描けません。こんなに小さな布なのに、何やらえらく複雑そうです。
これは困った、という顔をしていたら、「まぁ、現場見てもらうのが早いんですけど」と助け船が。ぜひ、と案内してもらったのが、応接室から中庭で通じる工場でした。
日本一の靴下産地で御宮知靴下が旗揚げするまで
もともと靴下産業が興隆する前に、「大和木綿」と呼ばれる綿づくりが盛んだった奈良。
そこに明治43年ごろ、現在の広陵町に住む人がアメリカから靴下の機械を持ち帰り、農業の副業として一気に広まったのが、日本一の靴下産地の始まりでした。
その広陵町で靴下づくりを学んだという初代御宮知社長が、終戦後に斑鳩の地で旗揚げした「御宮知靴下」。
工場は事業が軌道に乗るのに合わせて増築を重ね、今ではまるで木造の古い校舎の中に機械がぎっしり並んでいるような、不思議な空間になっています。
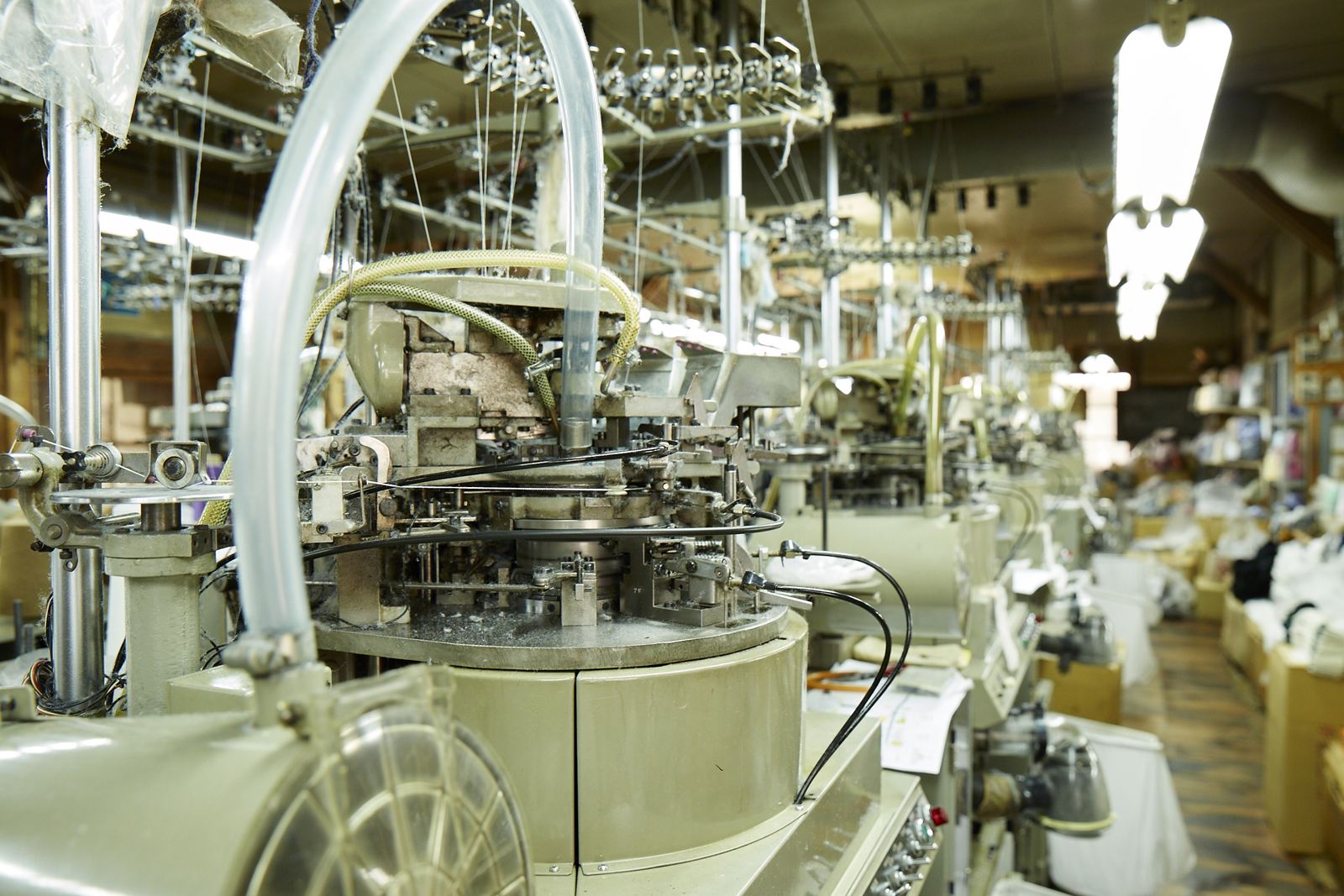
社長と工場長の間柄
「今ある機械は25年くらい前のものです。最新の機械はもっとコンパクトになって1台でいろんな靴下を作れるようになっています。
そうですねぇ、古い機械のいいところは、自分の技術で変わったものを作れる、というところでしょうか」
そう話す山下さんは、工場内の機械管理だけでなく、社長さんが各先から受けてきた「こんな靴下をつくりたい」というイメージを、実際の商品の設計や機械のプログラムに起こす重要人物。
もともと別の仕事で営業畑を歩いてこられた社長さんは、「私は技術がないんですよ」と控えめ。技術的なところはすべて山下さんに任せている、といいます。
たまたま開発中の商品の話が出た時も、
社長:素人考えかもしれへんけど、ここを無地にすることはできへんの?
工場長:いや、できるけどそれやったら一緖や(問題点が解決しない)ねん
社長:そうか、そうか
とこんな調子。
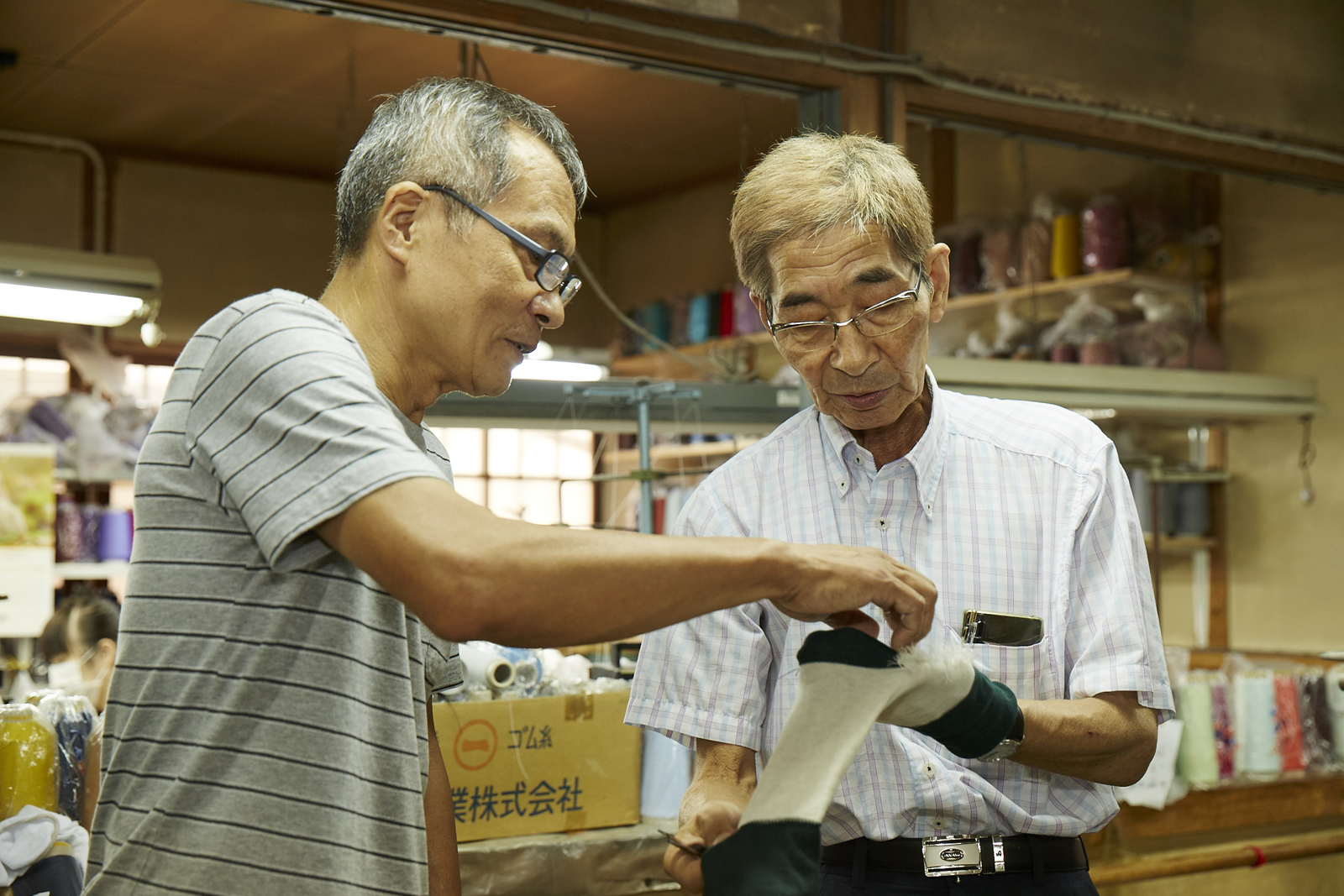
このお二人は立場で言えば社長と工場長の間柄ですが、靴下づくりの経歴では山下さんの方が先輩にあたります。
この「営業」の社長と「技術」の工場長が絶妙なペアになって、御宮知靴下さんのものづくりを進めています。(ですのでここから技術的な説明に社長さんは登場されません!)
山下さんの案内で、靴下工場見学がいよいよ始まります。
糸の道をたどって
「編み立てする目的によって、機械を使い分けていきますねん。太い糸を使う場合は太い針の機械を使います」
靴下は編み物。なので靴下をつくることを「編み立てる」とよく言います。
立てる、という言い方が、いかにも立体の編み物らしいです。
機械によって作れる靴下が変わるのですね、と返すと、ちょっと違うようです。
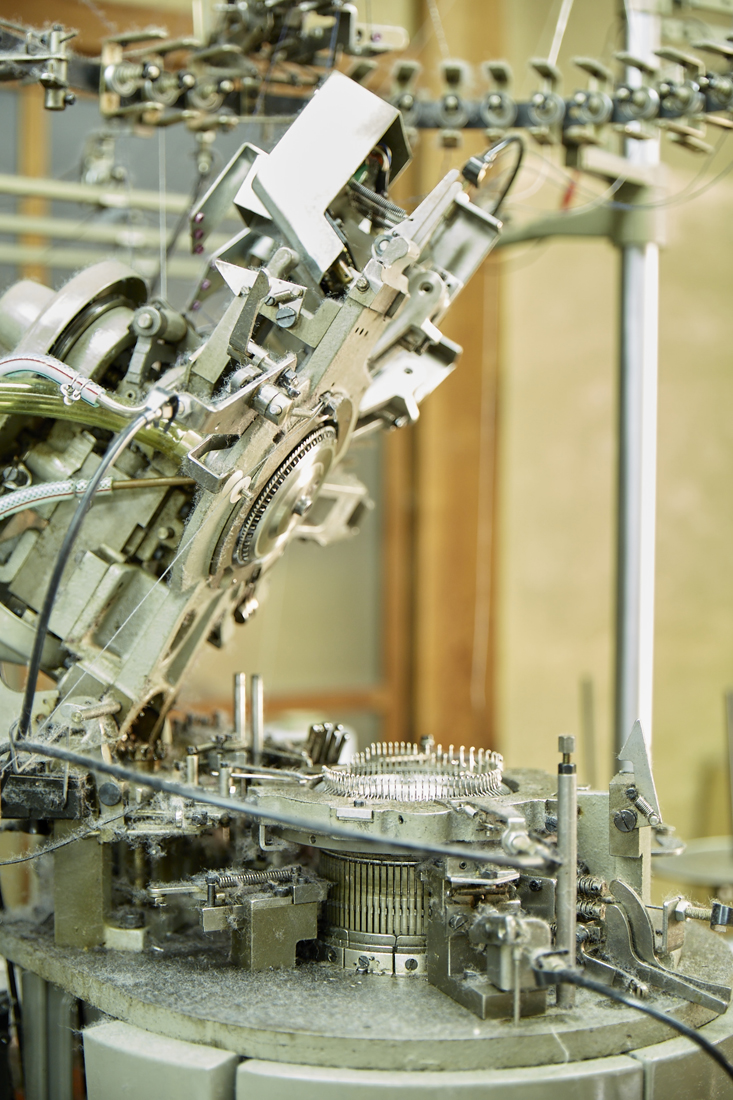
「機械に合わせて靴下をつくるというより、靴下に合わせて機械をセッティングします。
例えば子ども用と大人用では針数が変わります。厚手にしたいか薄手にしたいかでも変わります。例えば薄手のものは180−200本、という具合です」
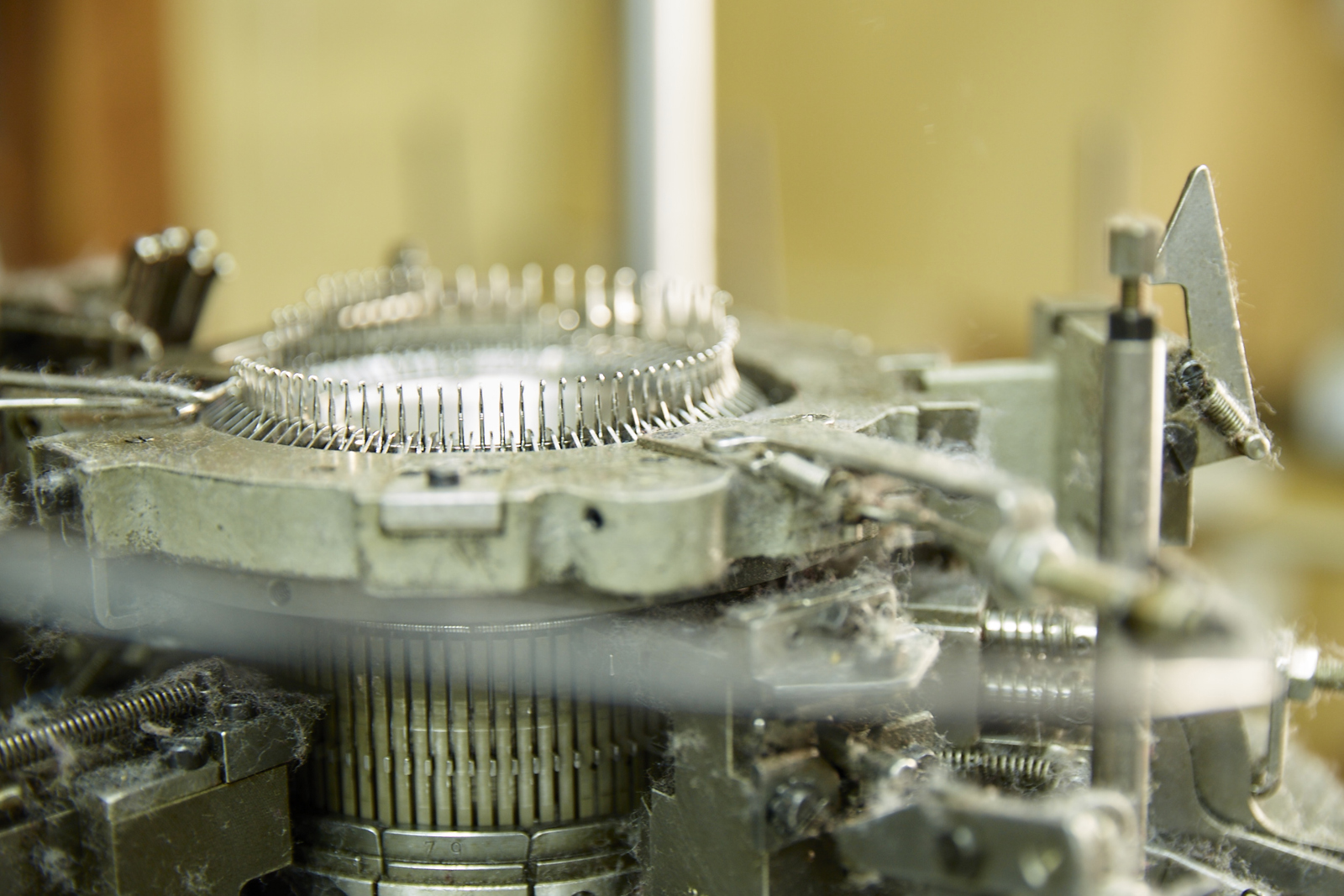
ミシンの針は通常1本ですが、靴下を編む機械は100を超える針が同時に動きます。
糸を通す針の本数が多いほど、生地の密度は濃くなります。この糸が通る道筋を、糸道(いとみち)と山下さんは呼んでいました。きれいな名前です。
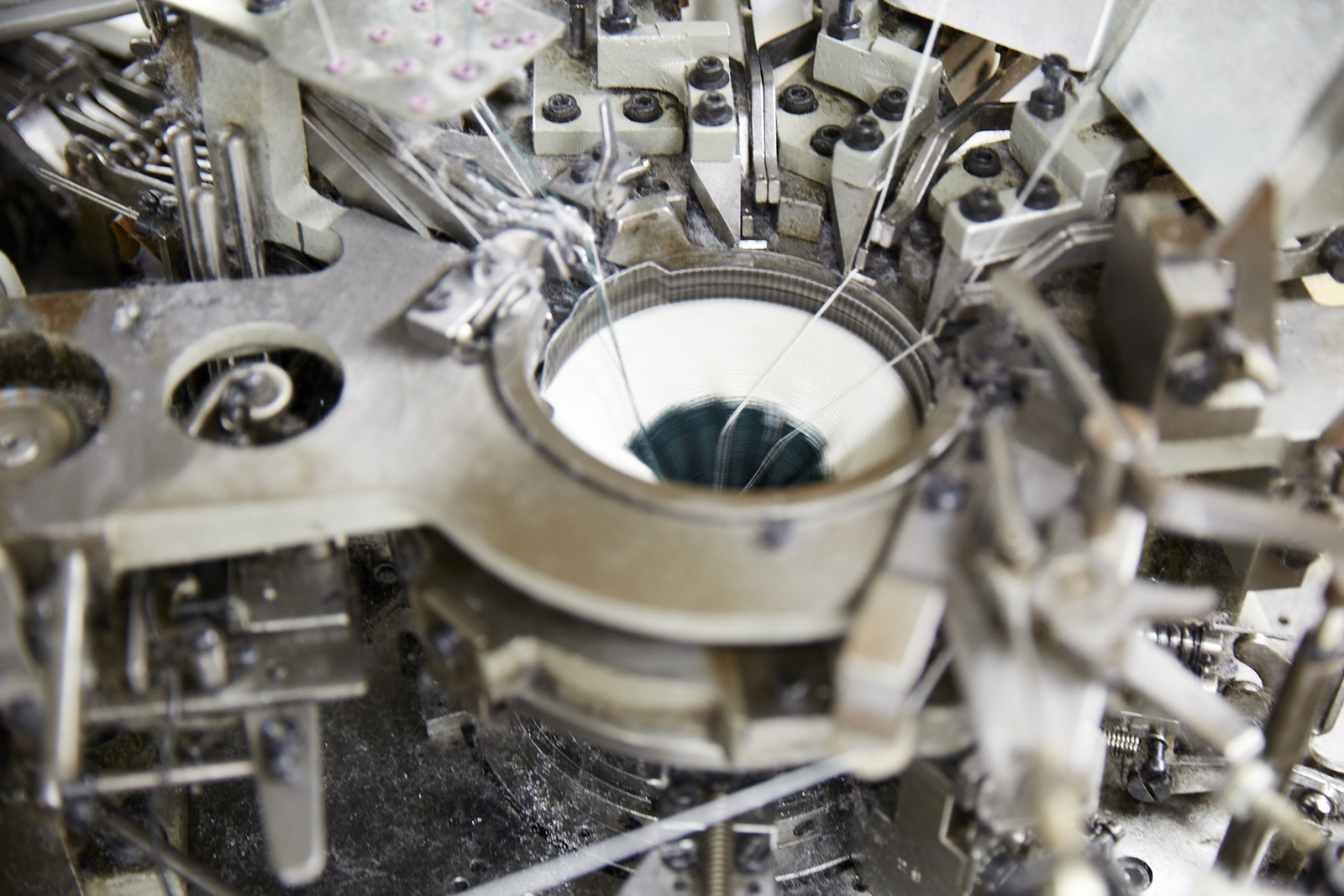
機械の上部には糸の供給源となる糸巻き(コーン)がたくさん。
あれ?これ、動いているものと動いていないものがあるようですが?それに同じ色なら、一つのコーンで良いのでは?
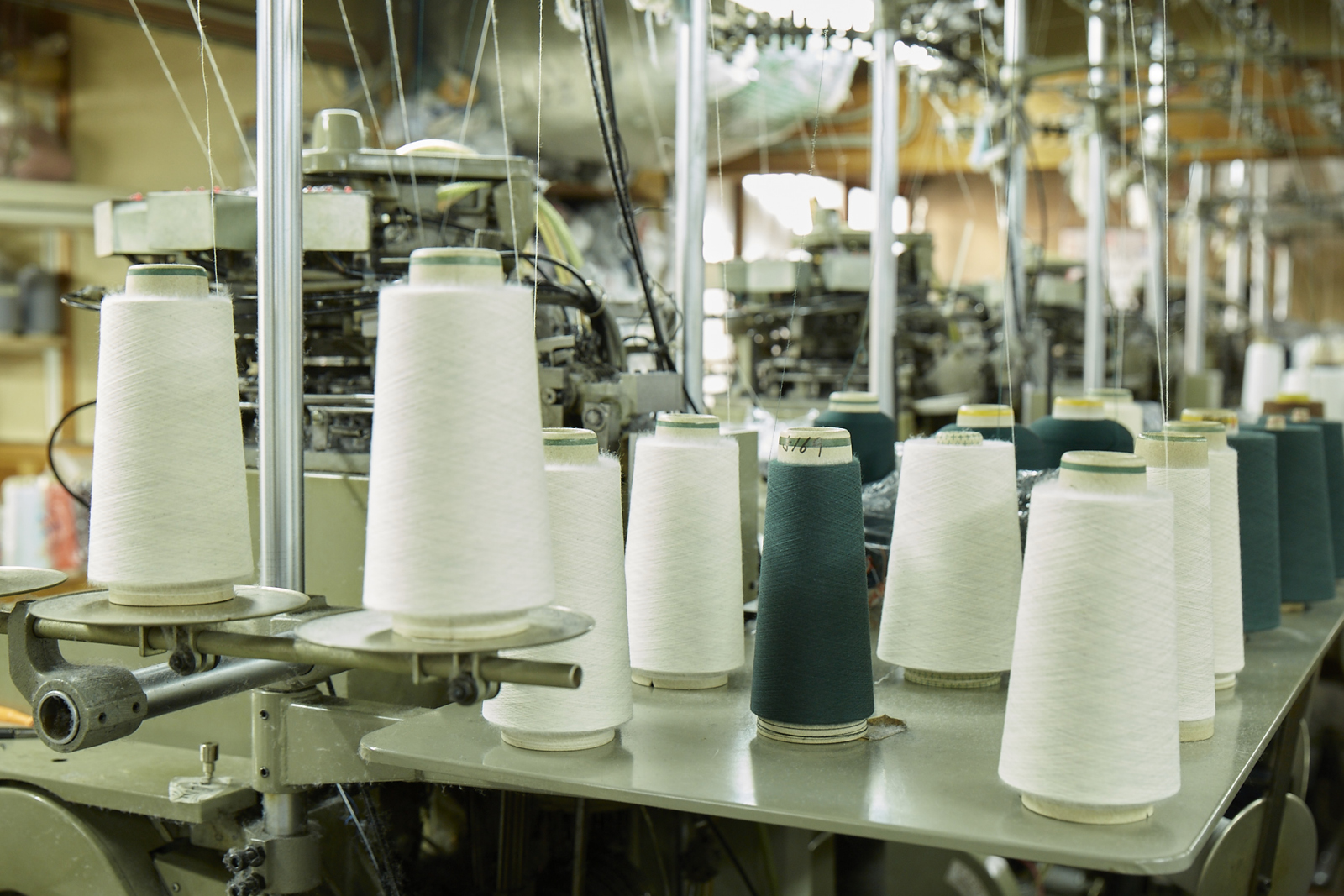
「コーンがセットされているそれぞれの場所に、プログラムが組まれています。
編み立てがある段階まで進むと、『今そこを編みなさい』と指示されたコーンが動くんです」
指先部分や足裏を厚くしたり、履き口をしめつけないよう工夫したり。靴下は衣類の中でもとりわけ機能性がしっかり求められます。
確かに、すぐに指先に穴が開いてしまう靴下や、くっきり跡がつくほど履き口をしめつける靴下は、がっかりしてしまいます。
ただ平坦に編んでいくのでなく、部位によって糸を切り替え、編み方を変えることで靴下の機能性を高めているのでした。
ホコリと湿度との闘い
「ちょっと待って、ホコリ取りますわ」
お話を伺っている途中、突然その場からいなくなってしまった山下さん。工場長、待ってください!
動きを追うと、近くの機械を手入れされていました。
当日の工場内はフル稼働状態。機械が動けば動くほど、糸から出るホコリが舞い、機械に付着します。たった1本でも糸道から糸が抜けたり切れてしまえば、不完全な編み立てになってしまう靴下。
機械の中に入り込んで誤作動を起こすホコリは大敵です。取材を受けながら、常に工場長は敵に目を光らせていたのでした。
もう一つ、靴下づくりの大敵がいます。それは湿度。
靴下は編み物なので伸縮します。湿度が高いほど、小さく縮まる。
編み立てている最中にも、もちろん湿度が左右します。乾燥の厳しい冬には朝と夜とでも仕上がった商品のサイズが違ってしまうそう。
「大手さんはだいたい湿度管理まで完璧にできる設備を持っています。うちは規模が違うので、機械にちょっとした調整を細かくかけていくことで、寸法を同じにするんです」
応接室でそう語っていた社長さんの言葉を、工場長が目の前で実践してくれました。
サイズが企画寸法に対して大きくなってきたら、これで調整します、と手にしたドライバーで示してくれたのが、度調機(どちょうき)。
ここのネジを緩めたり締めたりすることが、編む密「度」を「調」整するのだそうです。
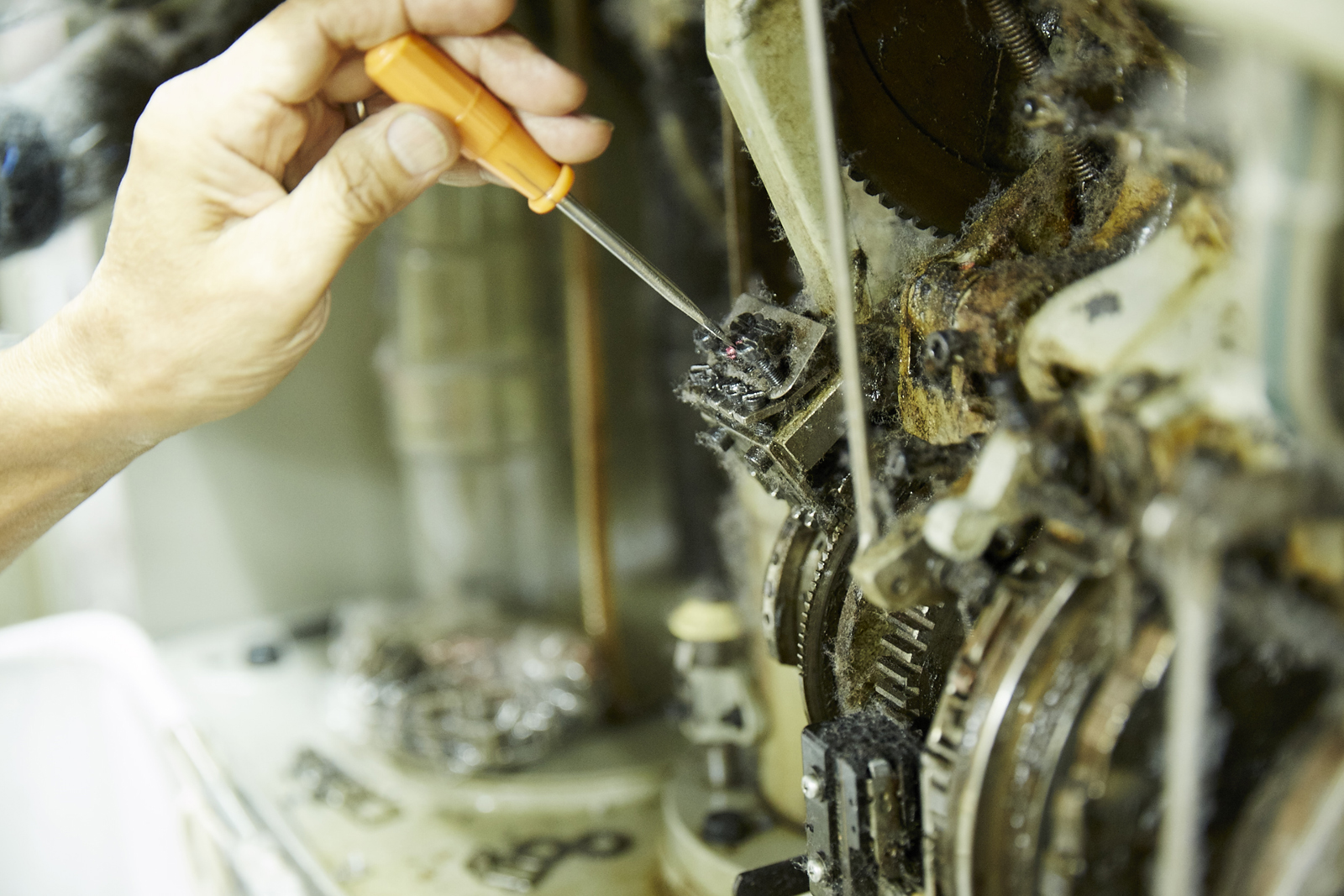
「これがわかるようになってきたら、いい商品がでけます。ここのネジがどの程度違ったら寸法が何センチ内に収まる、というのがわかってきたら一人前です」
商品のサイズを決める大事なパーツ。ここを勝手にいじることは、たとえ社長さんであっても絶対NGだそうです。
つま先が、ない!
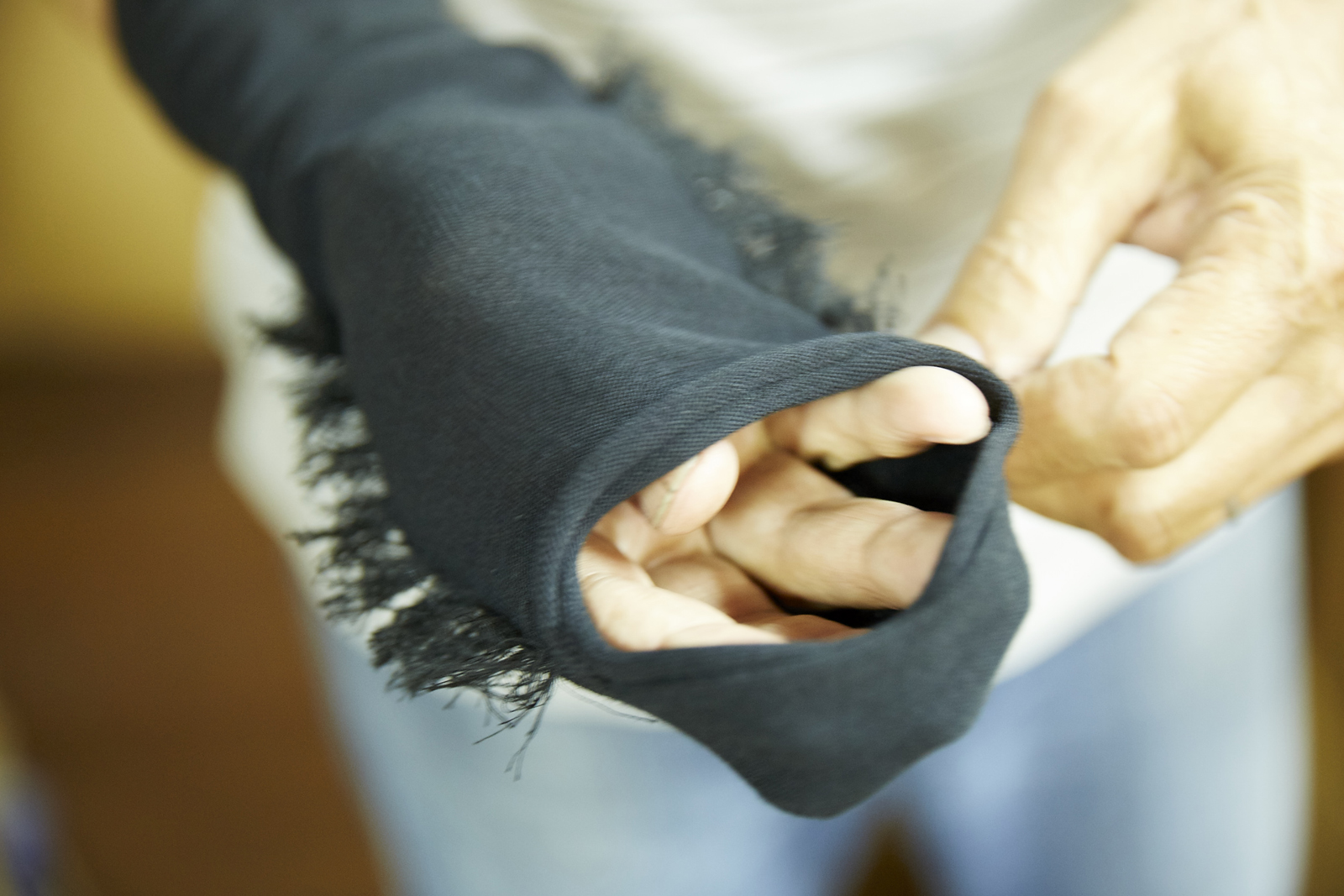
こうして無事寸法の狂いもなく編み立てられた靴下は、機械の下からシュポンと落ちます。見てみると、実はこの段階では、筒状。
機械は靴下を円状にぐるぐる編んでいくので、つま先はまだ閉じられていないのです。
ここで業界用語でロッソと呼ばれるつま先の縫製へ進みます。
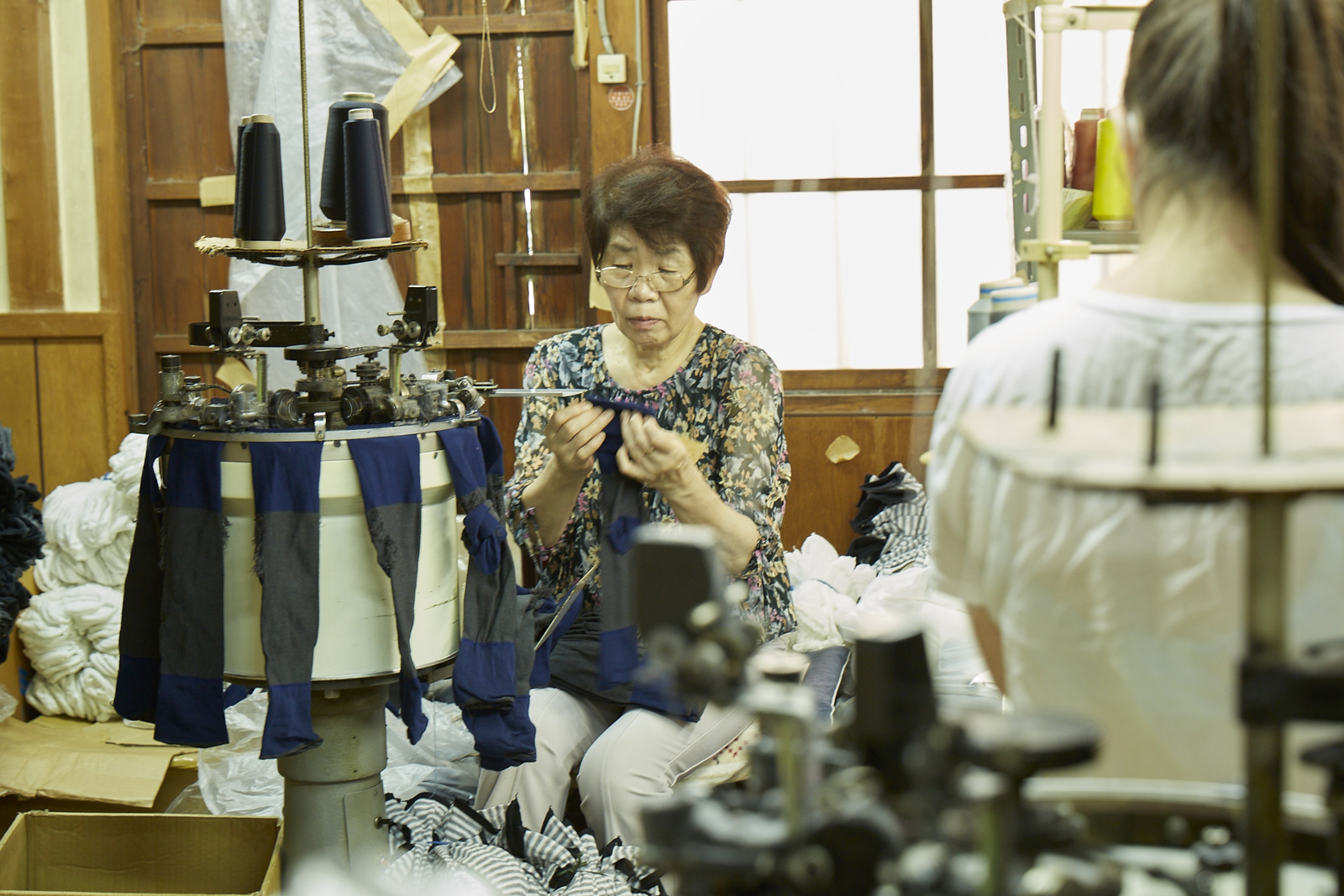
洗濯の小物干しのような形状の機械に、女性が靴下を挟んでいきます。
機械はゆっくりと回転し、その間に編み終わりの部分を縫い合わせながら上の余分な部分をカット。一周まわる頃には無事に靴下の形になっているという器用な機械です。
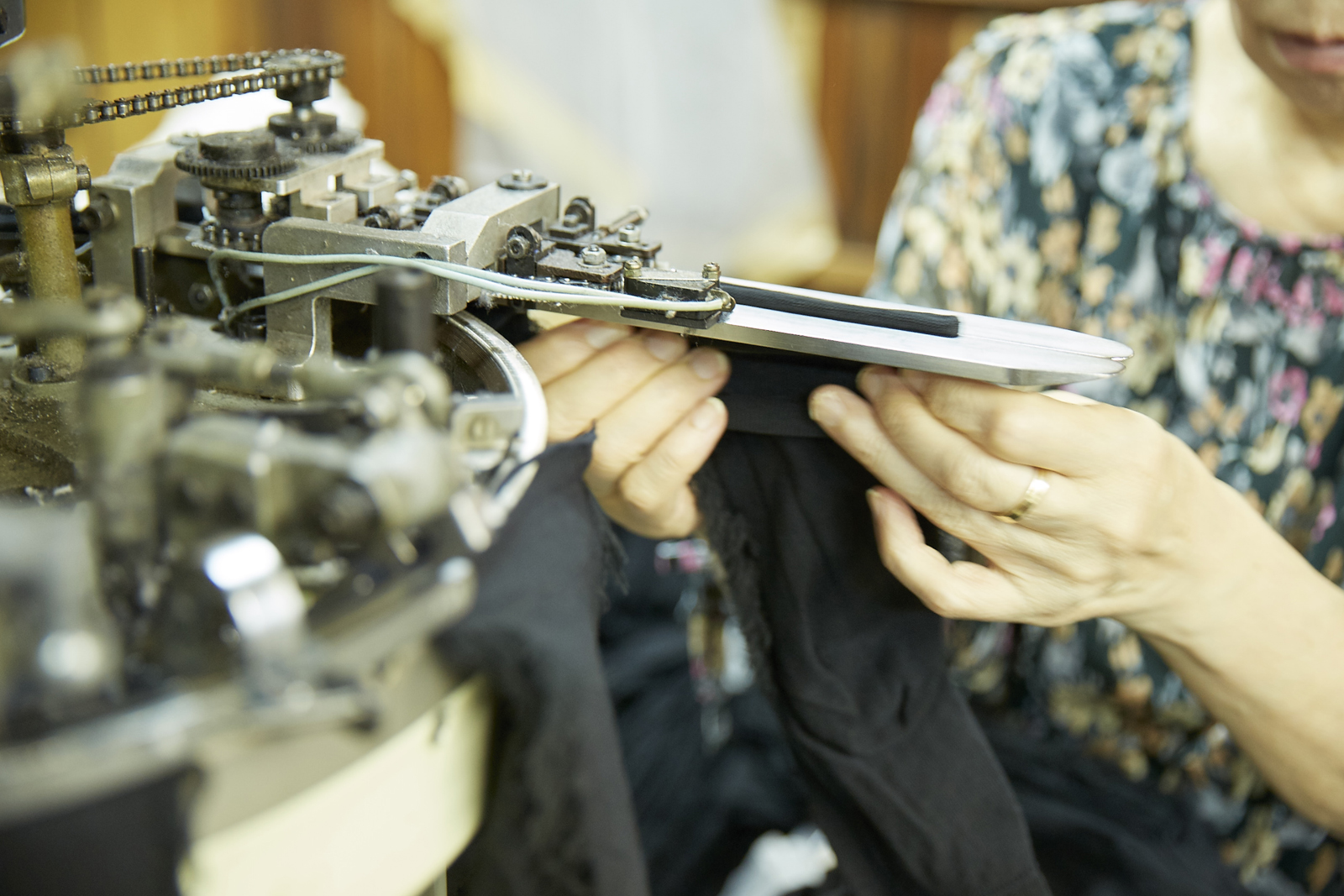
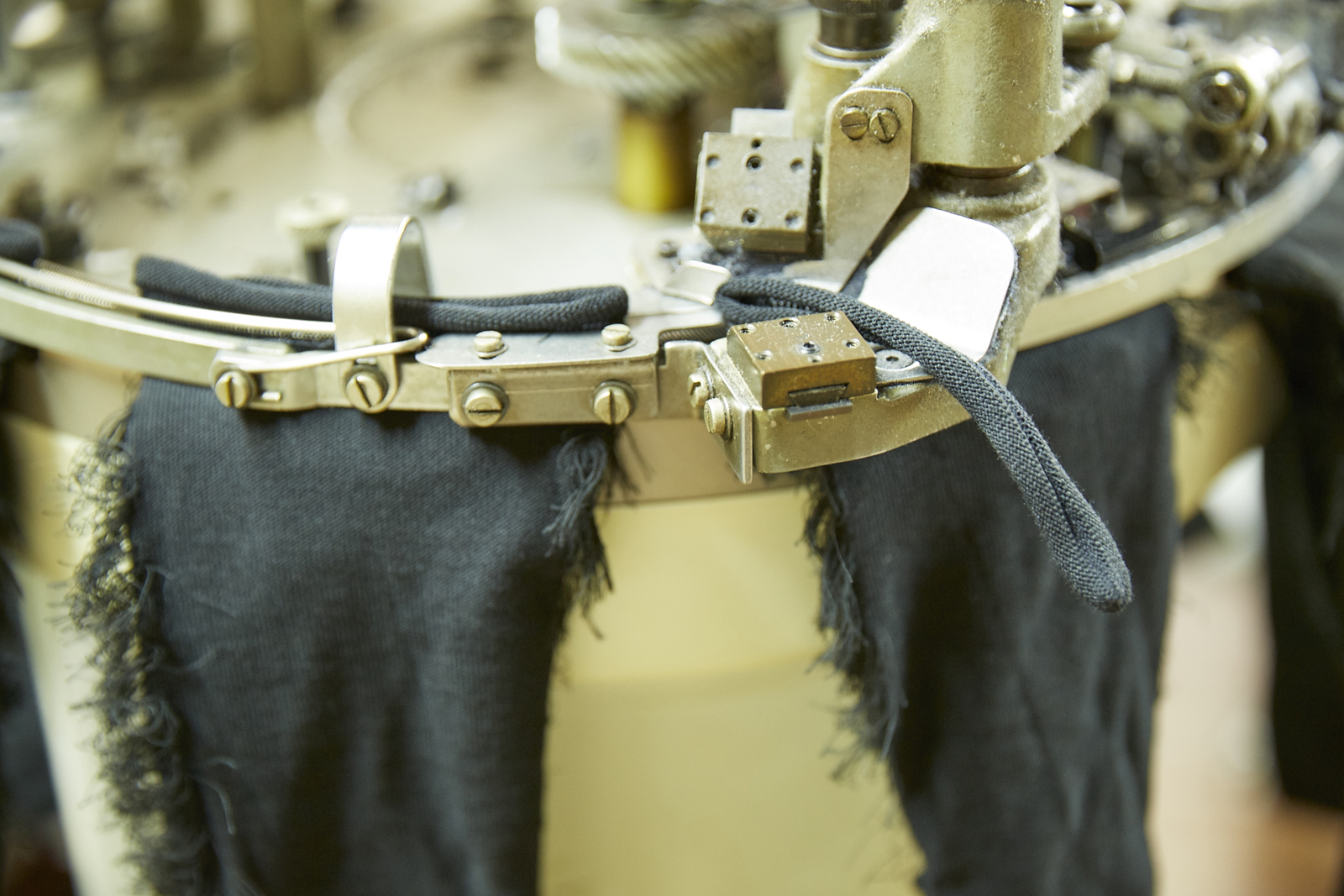
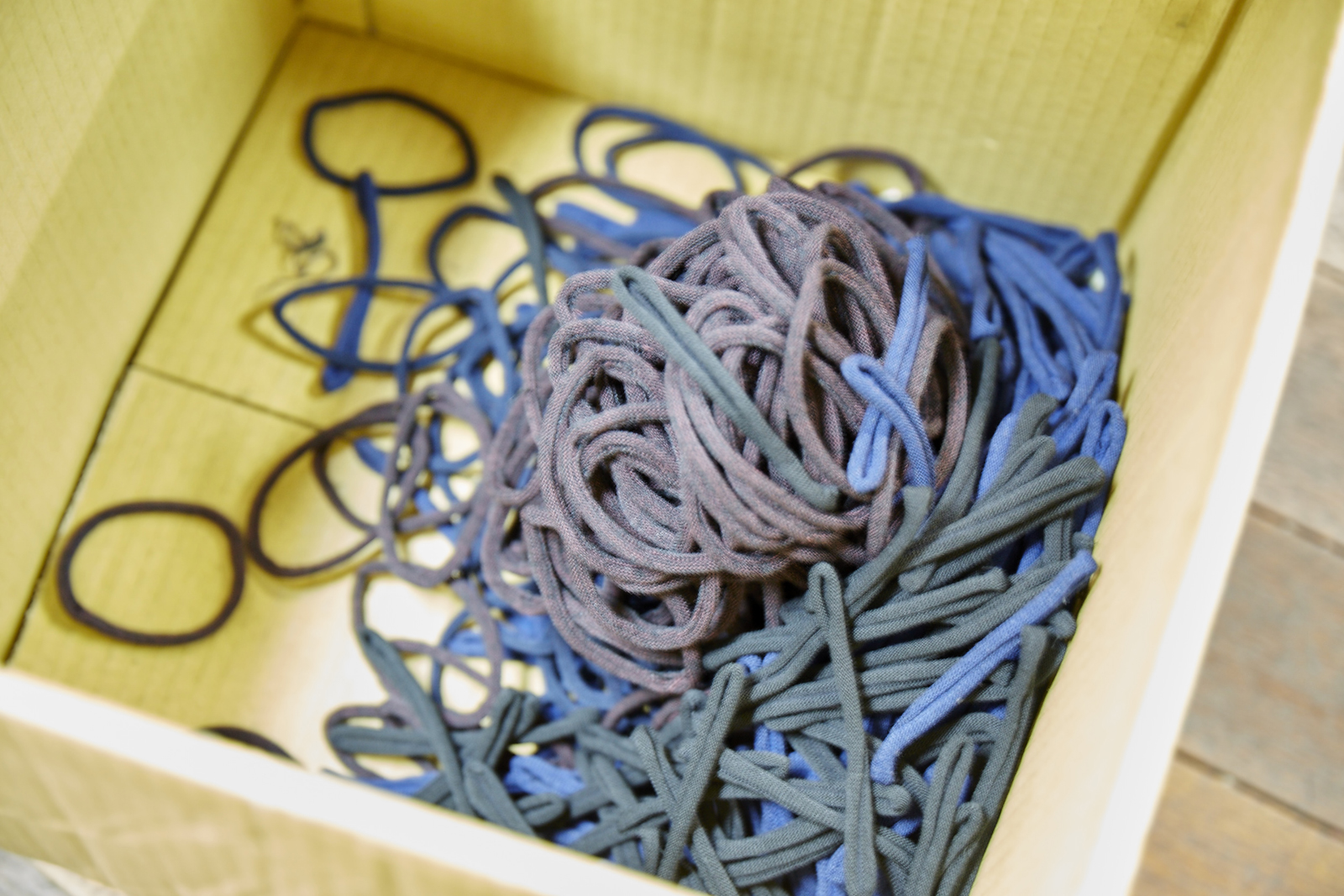
完成形に近づいた靴下はこのあと外部のセットやさん(筒状の靴下を平たく同じサイズに整形する工程)に出し、戻ってきたものを工場内の検品スペースで検品、資材の取り付けが行われて、商品の形になります。
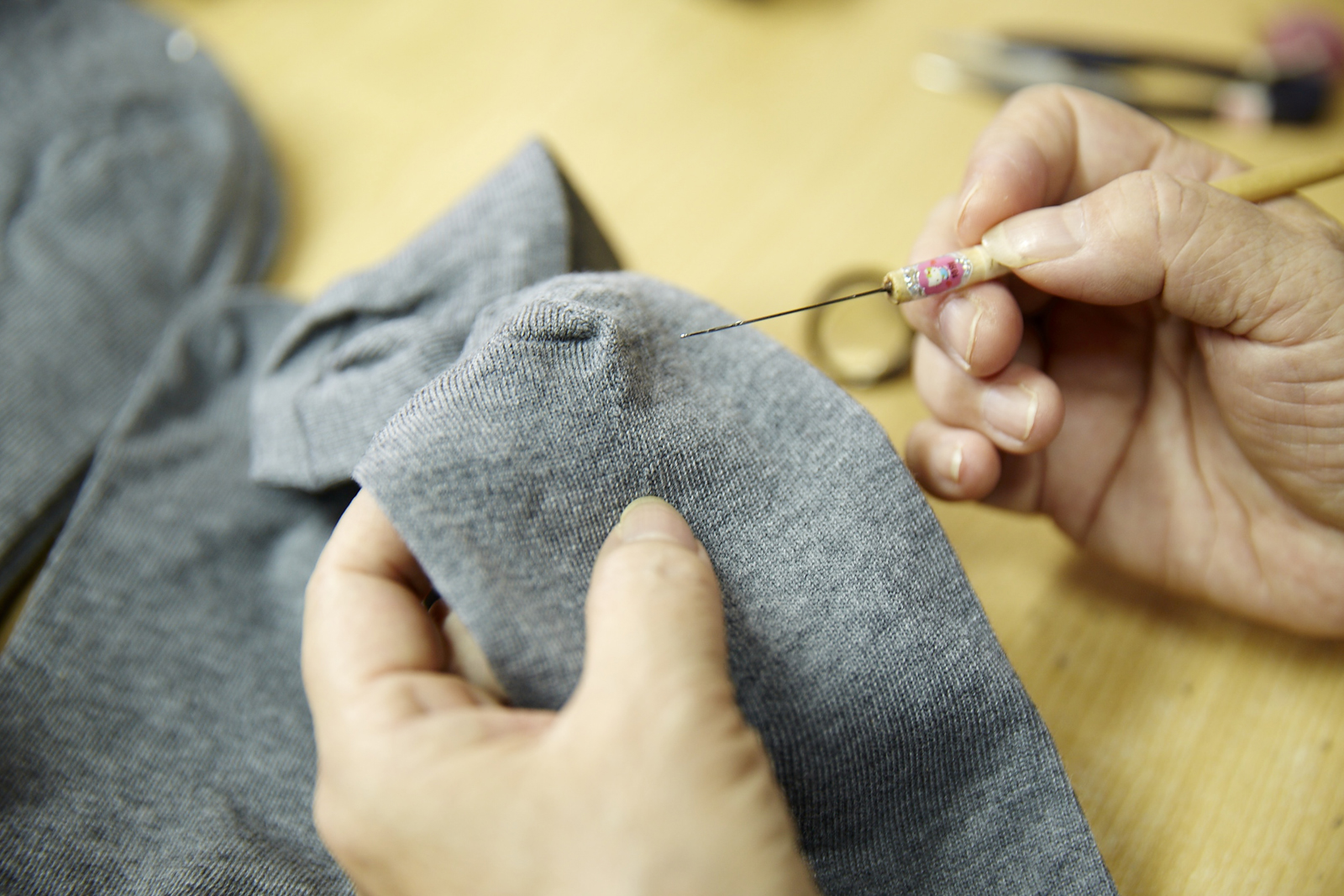
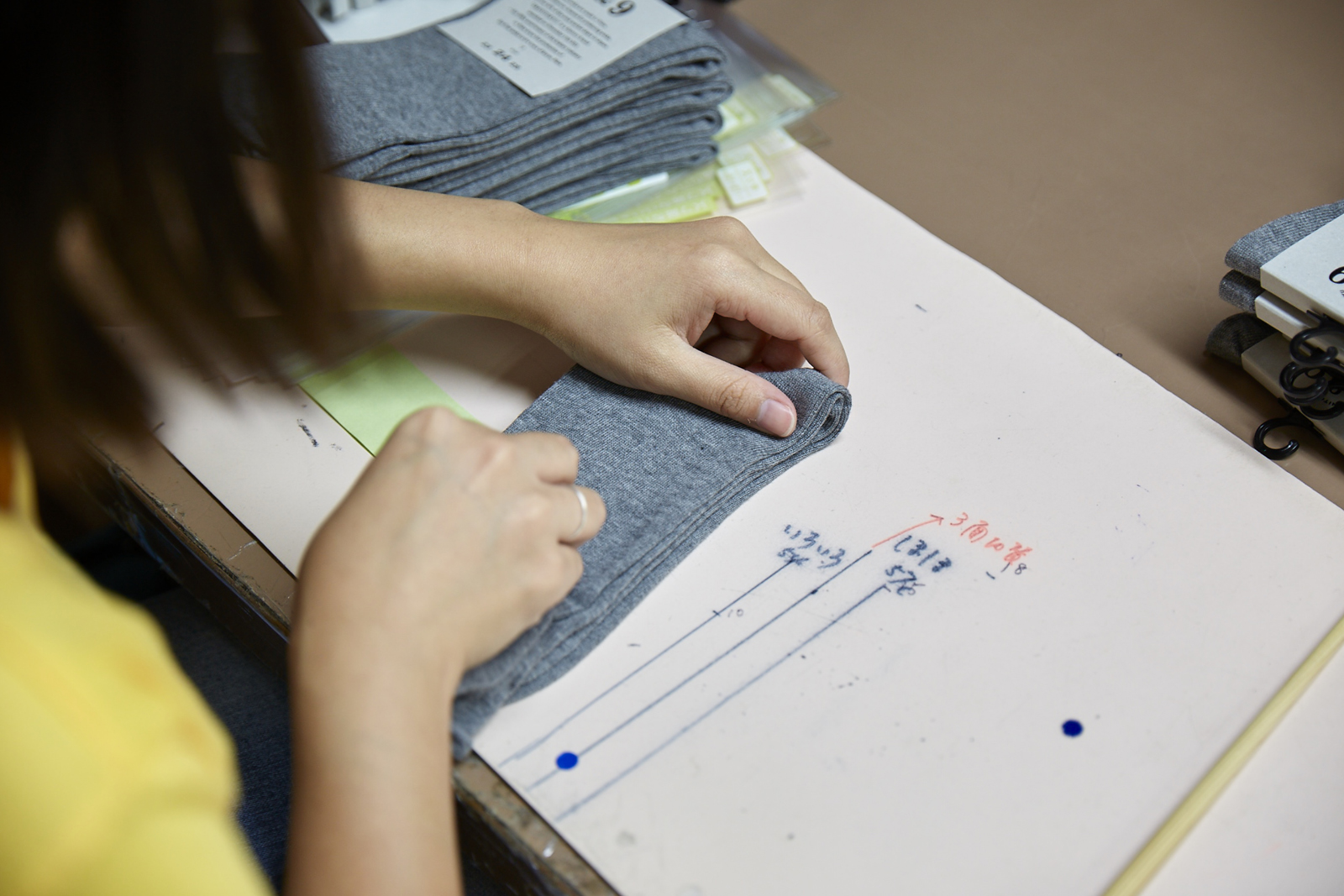
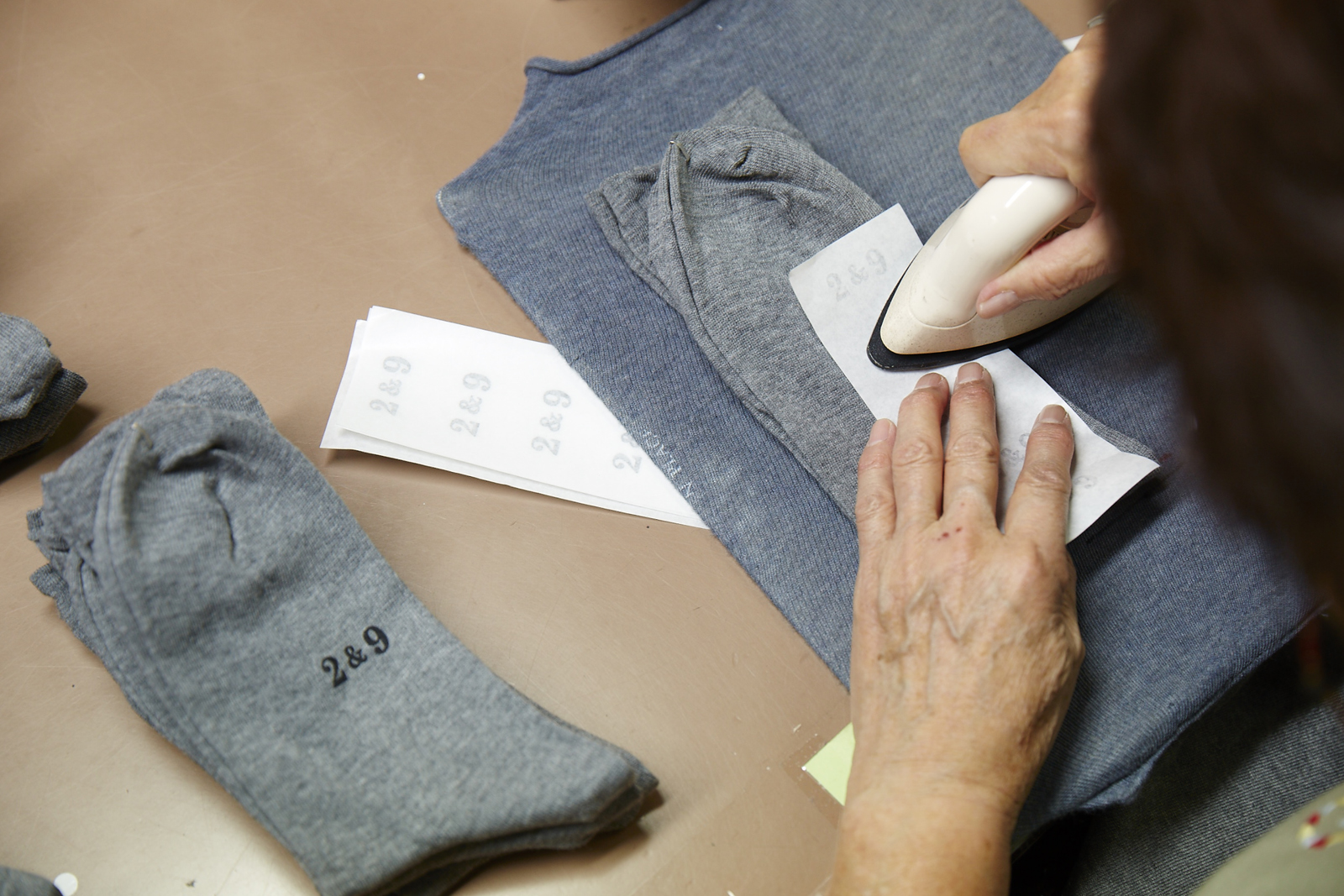
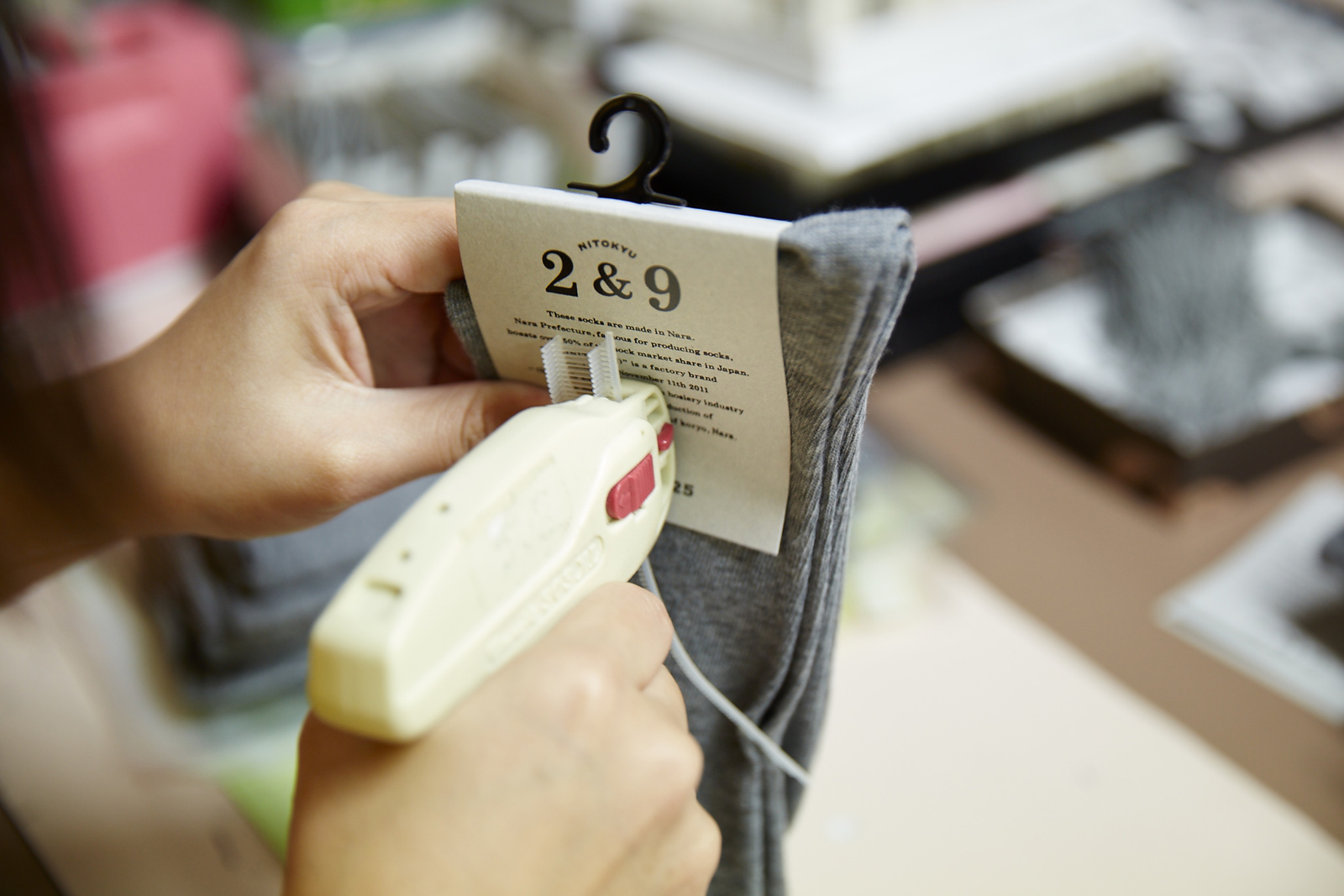
工場のホームドクター
取材中、再び山下さんの姿が見えなくなった瞬間がありました。
見つけた山下さんは、黙って真剣な表情。
「ホコリ噛んでますね」
??
「綿ボコリがここに詰まってます。こういうのが、寸法を狂わす元になります」
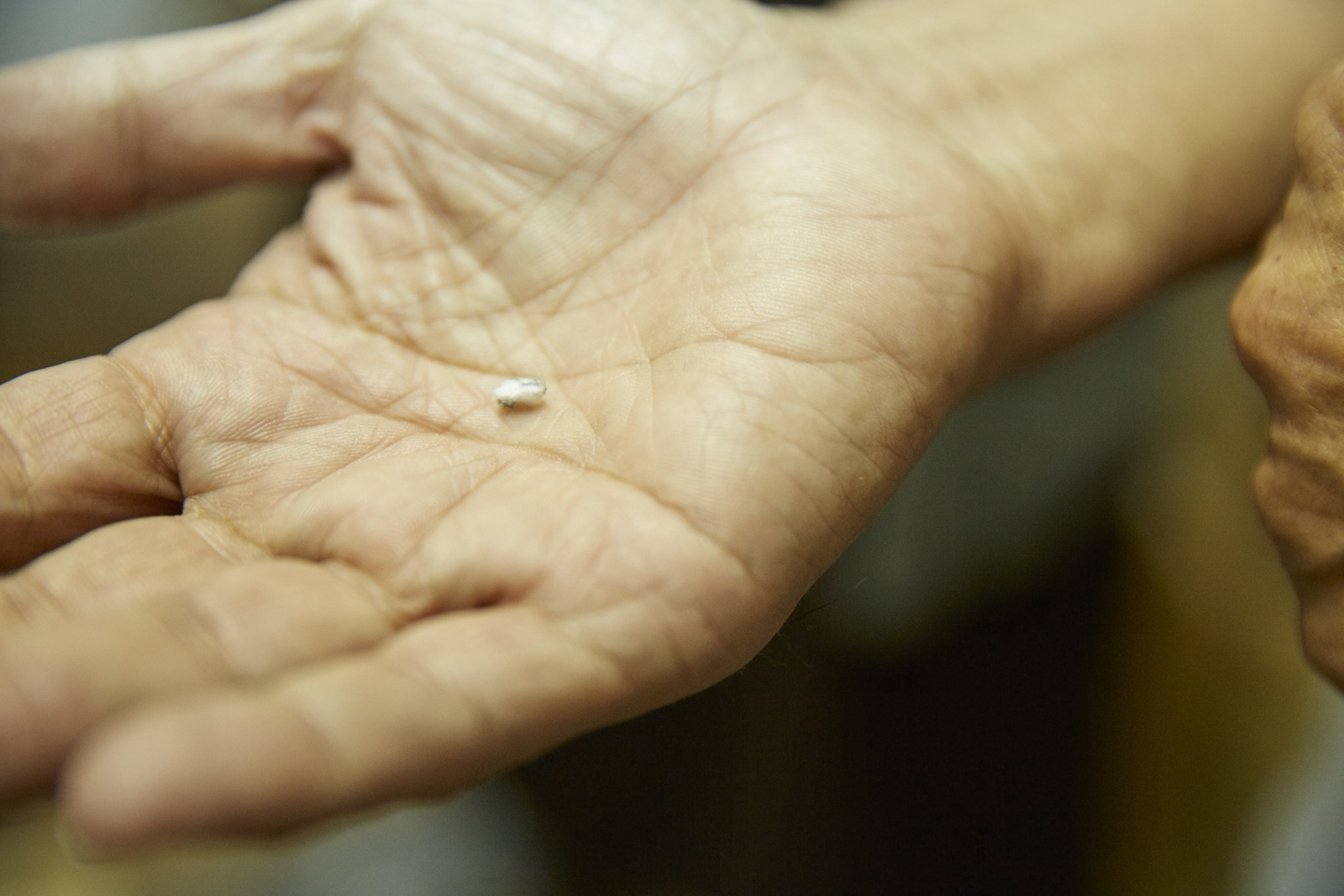
手にとって見せてくれたのは、小指の先ほどの小さな塊。靴下づくりの大敵、ホコリが玉になって機械内に入り込み、機械を止めてしまっていたのでした。
「長年やっていると、糸をちょっと引っ張っただけでね、あ、これ何か噛んでるなとわかるんです。さっきスタッフの子が見てはったけどまだ慣れてないもんやから、わからんと機械を触って、また糸が抜けたんです」
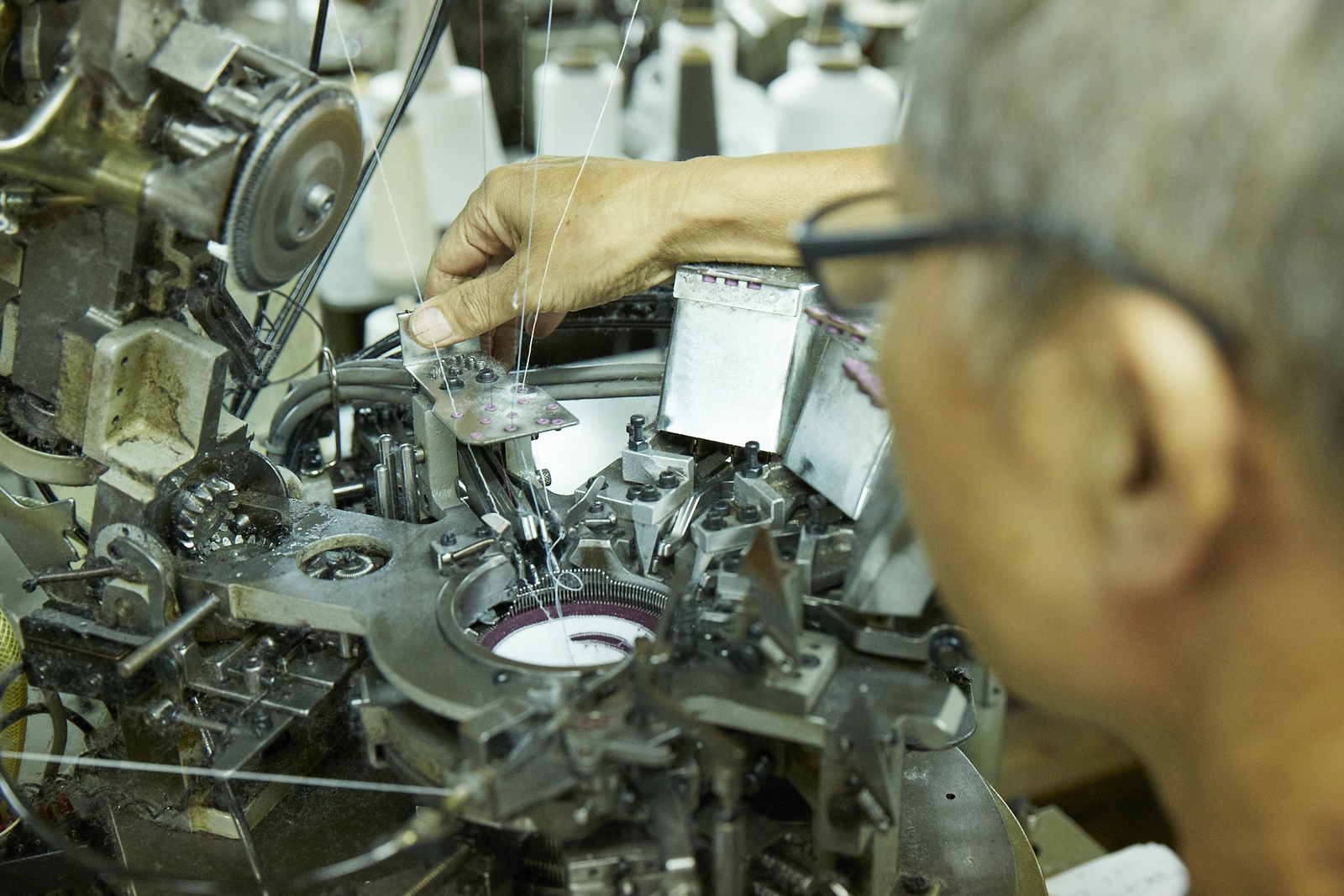
他のスタッフも気づかないエラーをすぐに見つけてしまう様はさすが工場長、信頼できるホームドクターのようです。
「工場内に必ず誰か一人はいて、機械を絶えずチェックする。それで商品が安定します」と語る山下さん。
細かな目配りを絶やさないことで、靴下づくりの無事は保たれていました。
毎日、褒められもせず苦にもされず、黙って私の足に沿い、動きを助けてくれる靴下。
この形になるまでの数え切れない「ひと手間」「ふた手間」のことを思うと、「いつもありがとう」とねぎらいたくなるような気持ちになって、工場を後にしました。
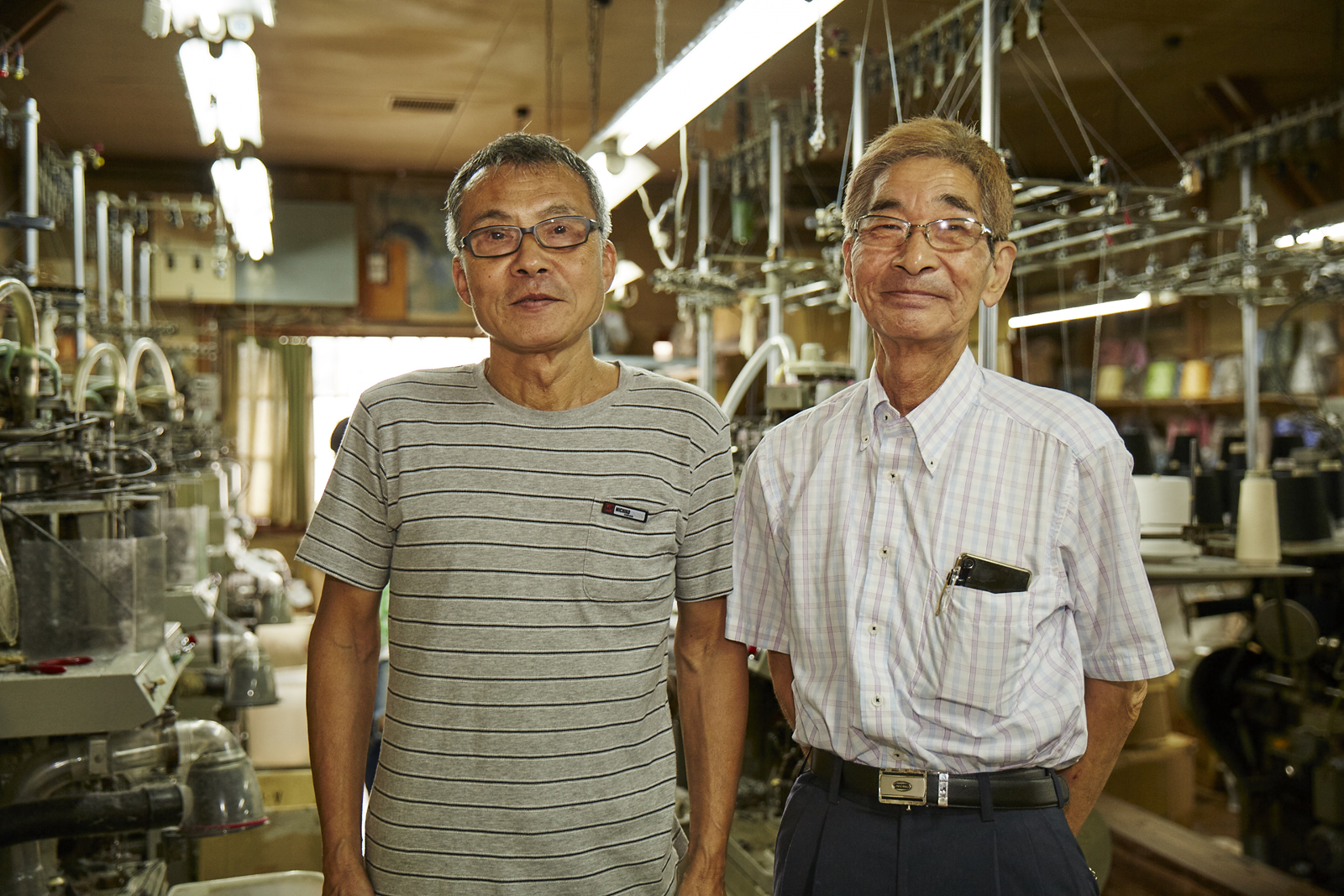
<取材協力>
御宮知靴下
<関連する商品>
2&9 しめつけないくつした
文:尾島可奈子
写真:木村正史
※2016年11月30日の記事を再編集して掲載しています。